Because of its influence on weight and cost, accurately digitizing the wiring system is a priority when implementing a digital twin strategy in the automotive and transportation sectors. It’s also one of the most challenging aspects of this task.
In my earlier blog posts, I described the importance of a comprehensive and standardized data model and on the different viewpoints on it.
Today I want to focus on the resulting benefits for the various stakeholders in the process. And again, the use of a standardized data model is the key for the digital twin application and for the resulting improvements in process and usage scenarios of related tools. Let’s have a look at a few of these aspects:
Decoupling of process between OEM and Tier 1
A while back, the Tier 1 harness suppliers had to use exactly the same tooling environment as the OEMs they were working for. This meant that the Tier 1s had to invest in and maintain different toolsets for every OEM. Also, it was not easy to shift engineering resources between different projects without investing in training, and allowing for learning curves for the different toolsets.
Data exchange standards such as KBL have made it possible to decouple this process chain.
As a result, the Tier 1 suppliers can work in their preferred tool environment, which may be different from and independent to the tools used by the OEM. At the end of the day, all data delivered by the suppliers must arrive at the OEM in the defined standard format and with an agreed data maturity. Of course, it is essential to have a powerful viewer so all stakeholders can read, understand, and verify the KBL data easily. And we know that an XML-editor isn’t up to the job. That is why Zuken developed E3.HarnessAnalyzer with rich functionality to support this need.
Best-in-class tools for every process step
We continue on a similar theme. A digital process based on standards not only decouples the process between OEMs and suppliers, but also offers the opportunity to build a process chain within a company by combining tools from different vendors. This means, instead of having a complete toolset from one vendor, users can now cherry-pick the tools from different vendors. For the tool vendors this brings more competition, but for the users there are many benefits such as much more flexibility and investment protection.
Let’s look at an example: We’ll assume a company has a toolset in place for the development of wiring systems. Typically, there will be a schematic tool, a 3D DMU tool, and a 2D harness design tool.
Now a new requirement comes up; the ability to try out design changes quickly in order to speed up the design process. This could mean finding out the impact on bundle diameters, weight or cost, for a planned change in the design.
The established tools can´t solve this issue, as their process is much too slow for a “what-if” evaluation such as this. On the other hand, there are no plans to replace the existing toolset in general.
The decoupling we looked at earlier allows the company to add a dedicated “helper” tool able to answer such “what-if” questions within minutes, to the existing process by using data standards such as KBL.
This use case is also a good example what standard interfaces have to realize: short set-up times. If a user want to run a “what-if” study, a major criteria is the length of time it takes until they can have all their series development data available. Previously, 80% of the time taken to run such a study was taken up on transferring, converting and adjusting the input data. Now a modern tool like E3.Wiring System Lab can support all applied standards and provides dedicated support functions, so a comprehensive data model for the complete wiring system of a car can be compiled in less than 10 minutes.
Keeping the topology in a 3D environment also saves work flattening to 2D, so after another 10 minutes, the results of the “what-if” question are available and the result is proven by a detailed data analysis generated by the system.
Such a flexible optimization of an existing process chain, achieved by adding innovative building block solutions, is only possible because of standardized data formats such as KBL and VEC.
Here’s another simple example for the resulting benefits around viewer tools such as the one I mentioned earlier, E3.HarnessAnalyzer.
In an OEM company there are many stakeholders who are interested in the technical details of a wiring harness. This could be production planners, EMC experts, quality inspectors or cost engineers. All of them need only read access to the harness data, so why make things complicated by making them work with authoring tools. And this is not only a problem regarding training, but also with access rights and available licenses. Using paper or pdf versions of harness drawings is not really a viable alternative. It is much better for all stakeholders to use a dedicated viewer able to render the KBL / VEC data in the way the different users are familiar with.
So the standardization of a digital data model is paving the road to make a digital twin strategy become true in daily practice, and to realize substantial benefits for the involved stakeholders.
Watch out for the next post in the series – Benefits of the Digital Twin Approach for After Sales and Service
Previous posts in the series:
Related Content
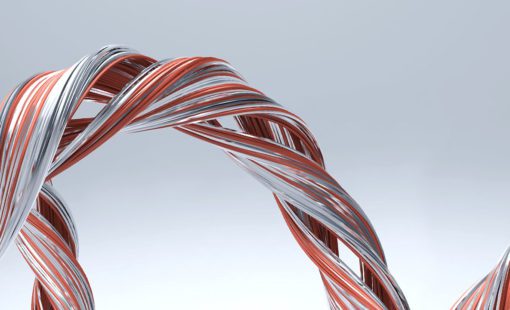
- Products
E3.series ermöglicht einen effizienten und präzisen Gestaltungs- und Fertigungsprozess für die Elektroplanung und Fluidplanung, die Kabelplanung sowie den Kabelbaum- und Schaltschrankaufbau.
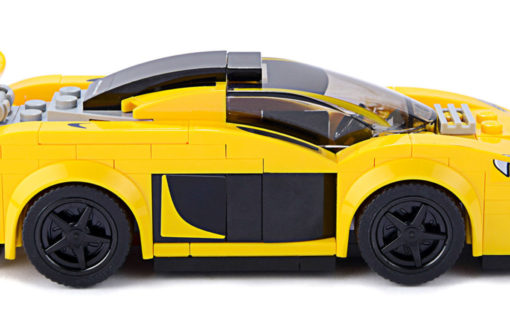
- Blog
Because of its influence on weight and cost, accurately digitizing the wiring system is a priority when implementing a digital twin strategy in the automotive and transportation sectors. It’s also one of the most challenging aspects of this task.

- Blog
While the concept of a digital twin has been around since the early 2000s, it’s only thanks to the Internet of Things (IoT) that its time has come. It was recently named one of Gartner’s Top 10 Strategic Technology Trends for 2018.