Industry 4.0, a.k.a. the Fourth Industrial Revolution (IR), is a hot topic because most of us are either taking our first steps in this world, or we’re preparing to.
Clearly, earlier industrial revolutions were all about making better use of resources (e.g. burning coal to make steam), people (e.g. workers in factories) and, latterly, electricity and computer-controlled automation. For each revolution, the companies that did well were early adopters of the technology and practices of the day, and they recognised waste when they saw it.
So, what’s going to be the secret of success under Industry 4.0?
My resounding answer is Data. Or, more specifically, making better use of data.
In the world of engineering, many companies store their design data within their organization’s Enterprise Resource Planning (ERP) system. But the ‘resource’ it focusses on tends to be people and materials. Because of this, most engineering departments also use complementary solutions for Product Life Cycle (PLM), Product Data Management (PDM), Material Requirement Planning (MRP) and Document Management Systems (DMS).
However, there often is an alarming disconnect between the systems I’ve just mentioned and the tools engineers use, such as MCAD and ECAD systems – especially, if we go beyond traditional mechanical engineering into the domain of cyberphysical systems that comprise mechanical, electrical and software components. We know this because of the huge amount of time we, as engineers, spend on admin tasks. At Zuken we had an idea that this was a big problem, from talking to our customers. Indeed, a study we commissioned last year revealed worryingly that engineers spend only around half of their time on core engineering tasks.
What is an Industry 4.0 company?
I’d define one as:
- Extremely dynamic, flexible and responsive to real-time market needs;
- Having no physical/geographic limitations, as it is connected to sister companies, partners and suppliers via the Cloud;
- Having seamless exchanges of data between all essential engineering design tools and PLM, ERP, PDM and DDM tool etc; and
- Actively discouraging emails and phone calls in relation to any given project.
So, imagine life within a company that has really bought into Industry 4.0.
All design activities create or modify data that is shared with others. All other stakeholders see their respective subset of that shared data. Also, providing suppliers and contractors with restricted views (of that data) means bidding can start the instant a design is finalised. Moreover, no one need worry about the flow of the data because automated processes will greatly reduce (and ideally eliminate) the amount of time spent on admin tasks.
Under this fourth industrial revolution, making poor use of data will be as inefficient as having leaky valve seals on a steam engine under IR1, living with faulty electric motors under IR2 and incorrectly programming production line robots under IR3.
Further reading
- Find out how under Industry 4.0, maintaining and upgrading plant and equipment will become easier by making better use of engineering design data, in Maintenance: A design for life , by Marco Canducci, Industrial Plant & Equipment magazine
- Engineering Data Management guidance from Zuken
Related Content
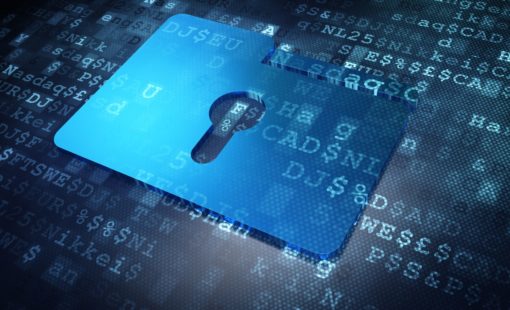
- Products
Das Datenmanagementsystem DS-E3 ergänzt die elektrotechnische Umgebung der E3.series. Sie verwaltet E3.series Projektdaten und Bibliotheken im Originalformat und unterwirft sie einem Engineering Workflow-Prozess
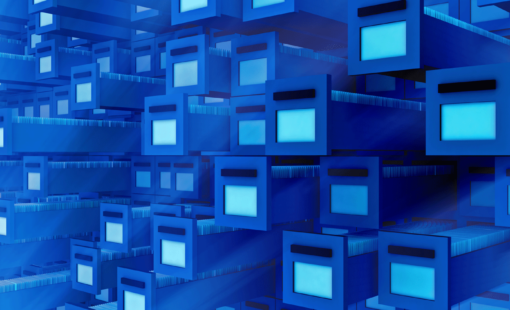
- Products
Zukens DS-2 ist eine ausgereifte, interdisziplinäre Engineering-Datenmanagement Plattform, die in Zusammenarbeit mit mehr als 3.000 führenden Unternehmen weltweit entwickelt wurde.
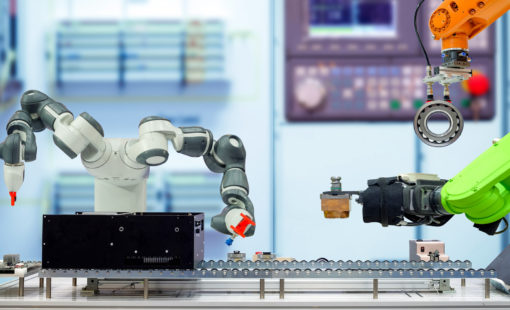
- Solutions
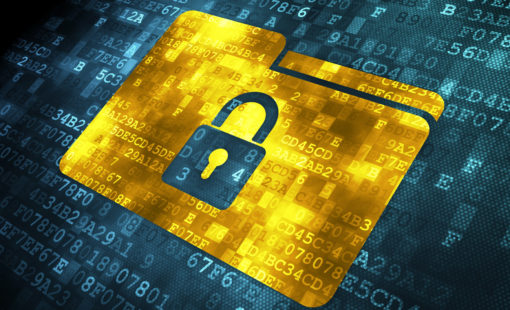
- Products
PCB Designdaten-Management. Standortübergreifende Verwaltung von Bibliotheken, Designdaten und Konfigurationen in einer einheitlichen Umgebung