With many manufacturers making the transition from traditional mechanical products to smart, connected ones, the collaboration between mechanical engineers and electrical engineers is more important than ever. They must work tightly together on the development of the board subsystem, the mechanical subsystem as well as the electrical subsystem to resolve competing requirements. Much to their frustration, manufacturers are finding that when these engineers don’t work tightly together, all sorts of things go wrong. Boards and enclosures fail to fit together at the prototyping phase. The wire harness has the wrong pinout. And let’s not forget thermal considerations.
In this post, we’ll give an overview of what Zuken is doing to address the design domain convergence described above. We’ve been working hard to improve both the CR-8000 and E3.series solutions to make collaboration between electrical and mechanical engineers easier than ever.
PCB based Collaboration
It’s undeniable: designers are packing more electronics into smart, connected products. Correspondingly, the trick in designing board systems today is figuring out how to find the right form factor, make sure everything fits and stays cool. There are plenty of other design challenges for board systems; these are the issues that lie at the center of collaboration between electrical and mechanical engineers. When coordination between these roles is lacking, there is a fallout in the development process. Don’t work together on fit? Then you might have an issue getting a door to close on the enclosure or a connector to line up with the enclosure opening. The hard news is that many of these multi-domain design faults are not discovered until a prototype is built.
Here at Zuken, we embrace a digital engineering approach. CR-8000 makes it easier to visualize board and enclosure designs in 3D. When you consider that CR-8000 operates on a native 3D kernel, it makes sense that you can create a digital twin of your board(s) and enclosure. CR-8000 imports an enclosure assembly from a variety of MCAD applications in STEP or a native MCAD format. CR-8000 supports the notion of a mechanical and electronic subsystem. The next step is to align the multi-board subsystem with the enclosure. You have a 3D view of the combined subsystems, which is essentially a digital twin. At this point, you can define a variety of clearance checks including board to enclosure or component to the enclosure. This is also where you have the opportunity to align enclosure openings with PCB components. Is that USB connector going to fit in the allocated opening? If everything looks good in CR-8000, you can export the board subsystem to your MCAD system for the final sign off.
Wire Harness based Collaboration
More electronics in products means they all need power and the ability to communicate with each other. It should come as no surprise that the amount of cables and wires in modern electrical systems is growing explosively. In the midst of all that complexity, electrical and mechanical engineers must collaborate together to verify compliance with critical checks and requirements. Complex cables or harnesses are more easily designed and verified in E3.series. But these large wire harnesses must be routed through complex mechanical subsystems like cars, trains, tractors, manufacturing equipment and aircraft. Doing this accurately to maximize fit ultimately lowers weight and cost. If this sounds like a digital twin for an electrical/mechanical subsystem you are right.
E3.series can exchange information with a variety of MCAD applications enabling this critical co-design capability. Once there, cables and wires can be precisely routed through the 3D product, optimizing for different cable paths and mechanical movement. With the optimal harness length and configuration set, that information is shared back with E3.series for final checks and generating manufacturing documentation. These capabilities can be utilized early and often in the design cycle, enabling collaboration between electrical and mechanical engineers.
Conclusion – Digital Twin Collaboration
Collaboration between electrical and mechanical engineers is imperative for the development of a wide range of products. Tight coordination between these roles ensures that boards fit into enclosures the first time and electrical systems deliver the right signals in the most efficient way. The gateway to a digital twin experience is having a connected 3D platform that can import/export and visualize multi-domain data. Zuken provides powerful innovative solutions that enable collaboration, early and often, between electrical and mechanical engineers.
Also see:
Related Content
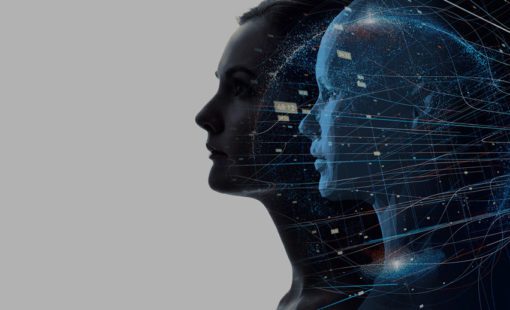
- Solutions
Many companies have recently embarked on the “digital transformation” journey to become more efficient and competitive. A recent IDC study showed that 90% of small and medium-size businesses are budgeting for the digital transformation and 73% have begun the process. .
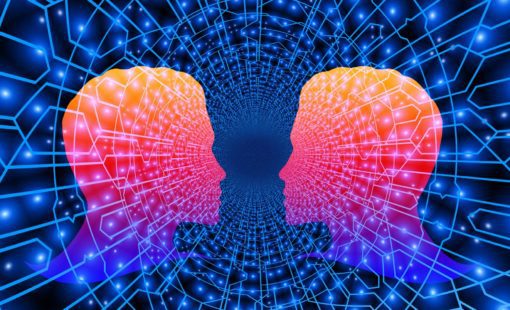
- Solutions