The Industrial Internet of Things (IIoT) is one of the great behind-the-scenes innovations of the 21st century. The IIoT allows for monitoring, analysis, and control of industrial systems to a degree never before thought possible. An IIoT system connects nearly all electronic devices in an industrial installation to the Internet. Such smart factory devices can include motors, valves, lights, sensors, switches, machines, and monitors. Digital, Internet-connected intelligence can now augment almost any component of the operation.
Edge computing is one of the newer additions to IIoT configurations. Computing on the edge means bringing distributed computing power out into the field—where operations are conducted. This trend reverses the early IIoT emphasis on centralizing the majority of computing power in the cloud. Additionally, Artificial intelligence (AI) is becoming a part of the IIoT with edge AI. Bringing more brain power to the edge results in faster response times and enhanced real-time capability.
The IIoT Promise
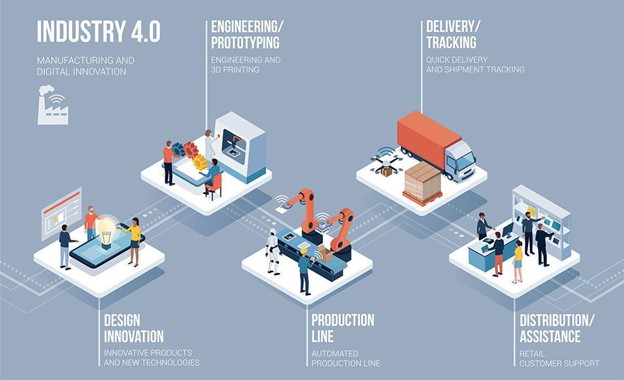
Increased production from equal or less input generates more significant profit and consumer satisfaction, leaving a smaller environmental footprint. With this in mind, the ultimate promise of the IIoT is to create a smart factory system. The IIoT allows automation, monitoring, and analysis to reach outside the building. It can connect the factory to remote suppliers, customers, and off-location management. These advances are paving the way for smarter, more efficient manufacturing systems, playing a critical role in the broader transformation brought by Industry 4.0.
In 1928, the Ford Motor Company opened the River Rouge plant—featuring auto manufacturing as one end-to-end system. Coal and iron entered one end, and finished cars drove out the other. This was the early 20th-century version of keeping operations under control. Today, the IIoT allows the same management and control even for globally dispersed operations.
The IIoT can connect and analyze all factors that impact reliability, efficiency, or performance. It can adjust systems in real time to adapt to environmental issues or supply disruptions. With the Internet, connection is global. For example, an alternate machine in Mexico can automatically compensate for a breakdown in Malaysia. The fully utilized IIoT system can even adjust workflow for the difference in shipping time.
Security Risks on an Industrial Scale
Along with the benefits comes risk. Connecting to the Internet introduces worldwide vulnerability. As an industrial system, the IIoT brings extra risks and requirements. Notably, security and reliability are more critical in an industrial setting than in a personal setting. At home, a poorly secured IoT environment can lead to a robbery. Poor security in a complex manufacturing plant may result in industrial espionage, plant shutdowns, or even fires and explosions. Public utilities are particularly vulnerable to Internet-enabled sabotage on a mass scale.
One of the most infamous IIoT security breaches hit Target retail stores in 2013. Cybercriminals accessed Target’s internal network by gaining access through the Internet-connected HVAC system operated by a contractor. More than ten years since the event, it still looms over large IIoT architects. Designers must understand that even the most minor, seemingly non-critical subsystem is a potential avenue for a breach. If it has an IP address, it requires the same eye for security as a networked PC. Security needs to consider not only the company-owned equipment but also any connected third-party IIoT systems.
Surviving in a Challenging Industrial Environment
From a physical perspective, industrial applications often come with a much harsher operating environment. Dirt, chemicals, vibration, electrical noise, corrosive atmosphere, and other factors create significant challenges for companies designing and manufacturing IIoT products. Wireless communications, especially high-frequency, high-speed wireless is susceptible to degradation. Walls, machinery, and electromagnetic interference from industrial operations all work against wireless connections. Furthermore, wired connections may need extra shielding and mechanical protection. IIoT electronics design and packaging must consider not only the desired functionality but also the conditions at the installation site.
Adding Intelligence to Legacy Equipment

We tend to think of the IIoT as the latest in high tech. However, any operation is a mix of old and new. The equipment needing connection may be decades old and nowhere near ready for replacement. At home, it may cost an hour or two of wages to buy a new internet-connected coffee maker. The same cannot be said about a 5,000-ton forging press operating since 1984.
Legacy integration can be challenging for IIoT developers. Equipment built in the pre-digital era may utilize crude analog computing systems or fully mechanical controls. Early digital controls running in the 1980s era of MS-DOS computers still exist. IIoT upgrades to older equipment may require reverse engineering. Mechanical valves and switches may need replacement with custom-designed connected replacements. Sensors might require creative mechanical hacking into equipment.
The Smart Factory System of the Future
The Industrial Internet of Things, combined with AI and edge computing, is creating a new class of connected smart factories. Monitoring, control, and analysis can encompass multiple factories, vendors, distribution, and other influence factors. However, industrial settings require extra caution and careful design practices. Security is as critical a component of the IIoT as is functionality. Often, the installation environment contains hazards and risks not seen in the non-industrial IoT. Further, an IIoT-based smart factory is frequently a combination of new equipment and, sometimes decades old, legacy equipment. The IIoT is transforming industry and, if properly implemented, will create a new paradigm in industrial and system-level smart factory operations.