Manufacturing wants to leap into the world of the Jetsons. But there is one small problem: every time leadership consults a compass, it shows a different way forward. At first, there was digital automation, which was soon replaced by digitization. Then—to the horror of spell checkers everywhere—digitization transformed into digitalization. Now the compass is pointing toward digital transformation for product development.
The compass is not to blame; it is trying as hard as manufacturing leaders to keep up with the location of true north. As the capabilities of computers and networks increase, new and better ways to work keep appearing. Change is no longer an occasional disruptive event; it is a constant operational imperative. Digital transformation for product development is more than a path—it is a rewrite of engineering and corporate DNA.
The foundation of digital transformation is the use of a single source of truth that is digital and holistic, encompassing every part of the product development process.
What is digital transformation?
A digitally transformed company uses a single definition of system design housed in one location. That one definition and that location are virtual, and the definition is infinitely accessible to all who need to know and do based on the information found in it and added to it.
The specifics of the single definition vary. A single definition for the mechanical design of an enclosure need not be in the same location as the schematics. But a single definition of requirements for both is available across the company. Those who need both have access to both.
The overarching goal of digital transformation for product development is to use smart, connected systems to create smart, connected products. Model-based development environments allow all participants full access to all data at all times (managed with attention to issues including regulations and security clearances). Functions, logical architectures, physical designs, and requirements all fit into a more holistic process model of engineering workflow.
In practice, product development becomes a path based on a single, repeatable, consistent execution of digital processes. Information comes to the engineer instead of the engineer searching for it. Engineering change orders become action items that self-attach to the workflow model for all to see and respond to as required. Prototyping is a workflow that springs forth automatically when product design hits a milestone. It won’t be long before such tasks as custom additive manufacturing (based on supply chain or customer needs) or placement of a unique blockchain address will become automated tasks in this transformed workflow.
Adherence to schedule is also part of digitally transformed product development. The new workflow closes the gaps that occur with manually executed processes.
What does digital transformation entail?
Digital transformation looks different in every company. The journey often starts with an effort to solve one particular problem and then lengthens as the company realizes they can apply the benefits of the new digital workflow elsewhere in the company.
There are no specific products to buy: there is no digital transformation in a box. Instead, it is more like a journey of challenges and awareness. Digital transformation is an overarching super-initiative encompassing a variety of efforts. Most digital transformation projects encompass concepts such as digital thread, digital twin, model-based systems engineering (MBSE), and simulation-driven design.
At the data level, a new process model is evolving whereby product data is both a digital thread and a digital twin. A digital thread means that the right information is connecting to the right place at the right time. It is an automated two-way flow of information.
MBSE is a way to use information domains instead of documents as the primary means of information exchange. The domains include behavioral analysis, system architecture, requirements traceability, performance analysis, simulation, and more.
Simulation-driven design entails moving simulation and analysis from the late cycles of product development to the earliest stages of design. Simulation software has been revolutionized in recent years. New tools are making these processes more accessible, both in ease of use and in hardware requirements. Now engineers test key physics requirements and design checks early enough to make changes before the design gets locked in.
What is the value of digital transformation?
When everyone in the organization and the supply chain have access to the same data without intermediaries, a digital thread workflow creates a virtual representation of the product called the digital twin. The thread is the data conduit for CAD, CAE, and BOM data; the twin is the resulting visual and virtual representation. Together they are the single, holistic source of truth that eliminates information conflicts.
The resulting strategic framework unites data for maximum value. And it affects all workflow elements, including as-designed requirements, validation and calibration records, as-built data, as-operating data, and as-maintained data.
In the typical project, emails fly back and forth with file attachments. Those files quickly become outdated as the project progresses, yet nothing prevents old data from being used by someone who doesn’t check their email often enough. In the rebuilt workflow of digital transformation, all communications flow from within the single ecosystem of the project; eliminating misinterpretation and confusion that so often lead to errors.
Time for a fresh look
Product development has become too complicated. But digital tools make it possible to simplify processes by starting fresh with a new conception of how product development works in the digital age.
The key is creating a single source of truth—not a certain CAD document or specific spreadsheet but a virtual, digital, and holistic model of the product and all the processes that go into creating it.
Today, it takes smart, connected systems to create smart, connected products. It is now possible to create a product development workflow, based on a single, repeatable, consistent execution of digital processes, that automates intervention and keeps all team members up to date.
Elements of digital transformation for product development include information models such as digital thread, digital twin, model-based systems engineering, and simulation-driven design. Uniting disconnected processes with these models starts with taking a fresh look at what can be accomplished using a holistic framework.
Related Content
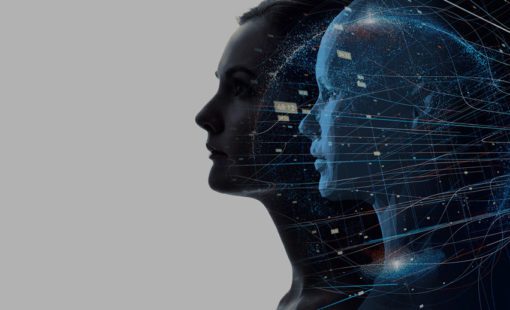
- Solutions
Many companies have recently embarked on the “digital transformation” journey to become more efficient and competitive. A recent IDC study showed that 90% of small and medium-size businesses are budgeting for the digital transformation and 73% have begun the process. .
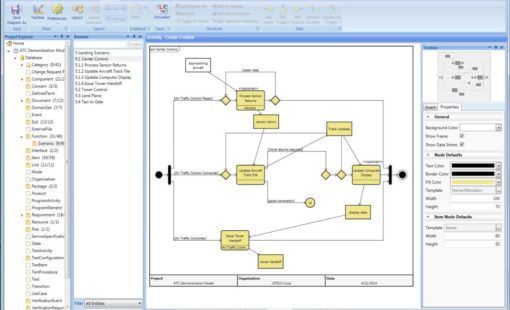
- Solutions
Digital Engineering requires a model-based design process that begins in Systems Engineering. Zuken acquired Vitech Corporation, a leader in Systems Engineering practices and MBSE solutions, with the intent of implementing an E/E model-based design process.