Smart and connected machines are the driving force behind Industry 4.0. Equipped with sensors, they continuously send data about their condition to analysis systems. These can then detect any signs of wear and tear and possibly even notify a technician before a shutdown occurs. This increasing complexity of modern machinery is a growing source of uncertainty for manufacturers. It entails higher risks in quoting, development, and manufacturing.
Modular product portfolios are designed to make the calculation and manufacture of capital goods easier to plan. They are a universally recognized approach to keeping pace with the growing product and process complexity in the long term. Breaking down something big into smaller single building blocks, such as modular PCB and modular wiring parts, makes a complex system manageable again. In addition, strategic flexibility increases because organizations can outsource individual building blocks to respective system partners. Nevertheless, product modularization often fails because of poor coordination between engineering disciplines.
To deliver on the promise of a modular product architecture strategy, companies need to create a number of prerequisites. In the area of organization, process, and infrastructure. In our white paper “The Modular Approach – A guide to multi-disciplinary success” we take a look at the resulting tasks from an electronic, electrical and fluid engineering perspective and present a pragmatic solution approach.
Complexity blurs the Boundaries between Engineering Disciplines
In product development, we understand modules as functionally and physically discrete units that we can combine or configure into an overall product via interfaces to other modules. Whenever one discipline can describe the entire product – a solely mechanical, electrical, electronic, or software product – modularization seems simple.
In mechatronic products, these physical boundaries are blurring because the functional units are interdisciplinary. Nevertheless, in most companies today, engineers develop mechanical, electrical, and electronic components, as well as software, in separate departments. In order to deliver on the promise of a modular product architecture, it is worth considering creating cross-disciplinary module development teams that work together on functional units with mechanical, electrical, electronic, and software components.
One emerging approach is to assign the coordinating function of these interdisciplinary design teams to the IT department. It already has responsibility for all authoring systems used in the different departments. In addition, we can assume that IT has a certain degree of impartiality needed to monitor potential conflicts of interest between the different engineering disciplines.
In order to keep mechanical, electrical, and software development connected, it is necessary to map the product’s functional description. Likewise the derived product structure with modules and components, and the associated configuration logic in product development software. The leading suppliers of today’s PLM systems can seemingly achieve this requirement
Functional Characterization avoids Ambiguity
So if we want to provide a comprehensive description of a module, a PLM system must be able to cover the functional description down to the level of electrical components. Asking this level of detail from current PLM systems is a stretch. Their data models were mostly developed for the requirements of mechanical design and do not provide for such fine granularity.
The Best of Both Worlds
A viable alternative – not only from a pragmatic point of view – is a federated data management model.
Zuken offers a portfolio of such federated data management solutions for PCB and electrical/fluid design. Our software integrates design and domain data management into the ERP and PLM processes. The DS-2 platform provides the basis for a true electromechanical data model. It thus creates the prerequisites for the successful implementation of modular product concepts.
For more details, download our Whitepaper “The Modular Approach – A guide to multi-disciplinary success” or watch one of our on-demand webinars.
Learn more about DS-2 – engineering design data management software.
Learn more about DS-CR – PCB library and design management for CR-8000.
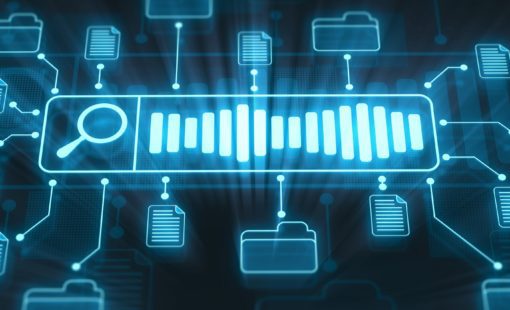
- Webinar
Who doesn’t recognise this? Many versions, many intermediate results, many copies, who has the latest version? Where is it stored? Who is currently working on it? Which settings, structure and database is the right one? We want to answer all these questions in this presentation.
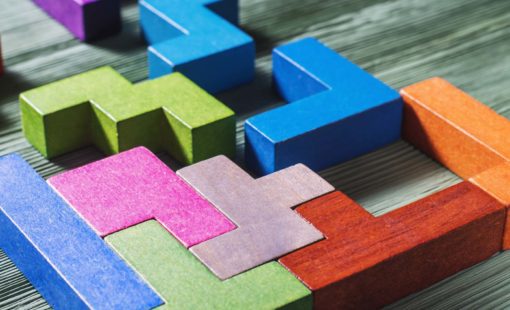
- White Paper
To deliver on the promise of a modular product architecture strategy, companies need to create a number of prerequisites in organization, process and infrastructure.