Printed Circuit Board design has been at the core of electronic innovation for decades. However, as technology continues to advance, PCB design faces new challenges that make it increasingly complex and demanding.
In an era where electronic products continually evolve to be more feature-rich, smaller and efficient, design engineers face the task of achieving higher performance while minimizing costs. This balancing act necessitates careful component selection, optimization of routing to reduce signal losses, dealing with increasing power demands of modern ICs (hence: more power-integrity rules) and consideration of manufacturing processes to maximize yield without compromising quality.
PCB Constraints are Growing in Numbers and Complexity Over Time
As the functionality of electronic devices increases, the basic laws of physics are still in place and impose strict limitations on how the signals on the boards propagate, interact, and dissipate heat within the circuitry. The miniaturization of components and the desire to cram more functionality into smaller form factors is leading to increased numbers of design rules and constraints.
Modern memory capabilities, such as DDR4 and its low-power versions (e.g.; LPDDR4) have become crucial across all industries, where they operate at exceptionally high speeds. Careful consideration is required to ensure that data signals reach the memory controller properly, effectively sidestepping potential timing challenges that might otherwise result in data corruption or loss.
Another driver of complexity, driven by cost considerations among others, is the practice of splitting planes or making plane cuts to distribute multiple voltages on the same PCB layer. However, this approach gives rise to irregularly shaped structures that can lead to the emergence of parasitic effects and resonances, significantly impacting power integrity and emissions.
As data transmission speed accelerates with USB, HDMI or PCI express technology amongst other things, signal integrity becomes a paramount concern, necessitating meticulous attention to impedance matching, parasitic transmission line effects (e.g.; losses, material roughness impact) and crosstalk mitigation.
The foundation of such data transmission standards are differential protocols that allow for the transmission of high-speed data streams through differential pairs. Yes, differential pairs require twice as much of the precious space (or more considering spacing and stitching vias and terminations, etc.) on a PCB but have the advantageous ability to generate minimal interference and their higher immunity to ground discontinuities and other noise effects.
Common High-Speed PCB Design Rules
Meeting the design rules and constraints imposed by these technological advancements is essential to achieve a functioning product that meets the required performance, reliability, and manufacturability standards.
The most common design rules in high-speed PCB design include:
- Length matching rules for differential pairs
- Traces crossing split planes, return current potentially guided by stitching capacitors
- Rules controlling the maximum allowed length for stubs (short trace segments to connect ICs or test-points)
- Routing of signals in parallel
- The impact of length differences within complex ICs and the necessity to compensate that on the board (if not using flip-chip technology)
The Importance of Virtual Prototyping in PCB Design
A powerful tool to navigate the new challenges is the use of virtual prototyping as part of PCB design. With the rapid pace of technological advancements, waiting for physical prototypes to identify issues can be time-consuming and costly. Virtual prototyping enables designers to simulate and validate their designs in a virtual environment to make qualified design decisions before committing to physical (mass) manufacturing.
This approach allows for early detection of potential signal and power integrity problems, thermal issues, and other design pitfalls. By harnessing sophisticated software, engineers can assess various scenarios, optimize component placement, and fine-tune routing strategies, all within a digital realm. This not only expedites the design process but also significantly reduces the likelihood of costly errors.
CR-8000 provides a comprehensive platform for simulating and analyzing PCB designs with embedded power and signal integrity analysis and electromagnetic interference checks. Whether you are working on a single-board or multi-board project, the software provides you with a complete set of tools to maintain the integrity and reliability of your PCB designs.
Conclusion
PCB design today is undoubtedly more challenging than it used to be. As electronic devices become more capable, the laws of physics remain steadfast, imposing rigorous limitations on signal propagation, heat dissipation, and component interaction. Mastering the dance between complexity, cost considerations, and integration is essential for creating electronic marvels that power our lives. Tools that enable constraint management and the simulation of different scenarios help navigate the landscape of modern PCB design.
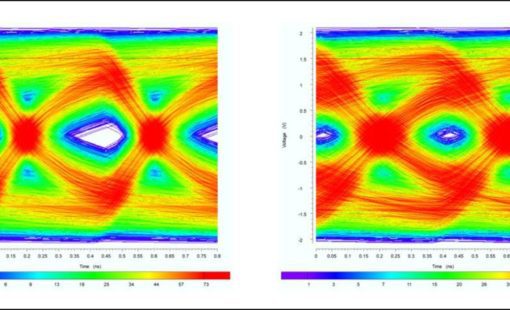
- Webinar
Using the example of the analysis of SerDes transmission paths such as PCI Express, SATA or USB3, we explain the methodology of an analysis- and constraint-driven assembly development with CR-8000 Design Force.
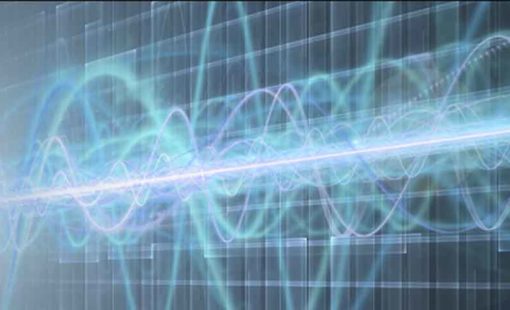
- Webinar
In this presentation you will be introduced to the necessary steps in constraining and validation of LPDDR4 on the basis of a real design realized in CR-8000 Design Force right first time.