Assembling a wire harness is a complex process. Zuken, in concert with our customers and partners, is tirelessly working to simplify the harness manufacturing process. As a matter of fact, the common theme in most customer requirements is to reduce the gap between quoting and delivering the project. Seeing that, Zuken’s primary goal with Harness Builder for E3.series is to empower harness manufacturers to achieve their goals. So, the latest partnership with Delta Sigma Company is a big step towards closing the design-to-manufacturing loop. Delta Sigma Company’s ProjectionWorks provides an augmented reality solution to simplify harness manufacturing. Now, Zuken customers have more smart manufacturing options available through the Harness Builder for E3.series application.
The joint webinar detailing the advantages of using augmented reality projection technology in harness assembly was a crowd favorite.
Some of the topics covered include:
- Using projection technology to drive the design-to-manufacturing process.
- Driving harness assembly with a step-by-step instruction process.
- Creating a dynamic assembly and manufacturing process.
Complexity in Harness Design
Let’s take a step back and look at the challenges in simplifying the design processes. Historically, capturing and reporting data from engineering to manufacturing used to be a tough challenge during the design process. The complexity stemmed from the need to maintain quality while reducing the time and manual effort to complete the tasks. Zuken introduced the Harness Builder for E3.series solution to simplify the harness design process. As a result, it is easy and seamless to capture and communicate rich data from engineering to production. What’s more, Harness Builder for E3.series provides the inputs to drive multiple manufacturing tools.
You can read more about the latest improvements in Harness Builder for E3.series in our what’s new 2020 blog post here. Some of the many data input options include:
- Automated testing machines
- Digital assembly aids
- Automated wire processing machines
- Labeling and printing machines
- Automated splicing machines
The next step in this evolutionary process is to improve the manufacturing process itself. However, to reach our goals quickly and easily we need to look at the latest innovations and adapt accordingly. It is important to realize, there is no one solution to the many manufacturing challenges faced by harness manufacturers. Firstly, we must take a holistic approach to find appropriate solutions. Secondly, we must start with intelligent design tools like Harness Builder for E3.series to drive innovative manufacturing solutions. Finally, we must combine the cutting-edge design system and a cutting-edge manufacturing system.
Simplifying Harness Manufacturing
A manufacturing technician relies on precise instructions to plan and layout a harness onto a nailboard or formboard. For the most part, the instructions are put on paper in the form of drawings, tables, and images. Given that the drawings are static in nature, there is a considerable amount of information packed into a small area. As a result, a congested drawing leads to time-consuming errors and rework. To emphasize, the answer is to simplify the harness manufacturing processes by simplifying the information delivery process.
Using a projection-based augmented reality system like ProjectionWorks from Delta Sigma Company is a game-changer. The ProjectionsWorks system did not originate with harnesses. The initial development goals for ProjectionWorks were to provide a low-cost solution to project clear and specific work instructions directly on an aircraft. Specifically, the Delta Sigma ProjectionWorks solution comes from years of automation work in the assembly and metrology processes involving the United States Air Force Research program and the F-22.
Reducing Manufacturing Overhead
The solution from Delta Sigma Company is proven to reduce manufacturing overhead by:
Augmenting outdated assembly processes
- Manage change by driving projection directly from Zuken design data
- Eliminate the need to print and reprint information
Reducing space usage with reusable nailboard
- Reduce set-up time and reuse existing boards
- No need to store every legacy board
Reduce employee ramp-up time
- Capture tribal knowledge in the digital process
- Simplify the training and ramp process
Reducing rework and errors by simplifying instructions
- Digital layout simplifies instructions
- Drastically reduce errors
Introduce dynamic work instructions and board layouts
- Progressively improve instructions and processes
- Step-by-step instructions reduce new process overhead
In conclusion, harness manufacturers must create accurate quotations/estimates, detailed error-free designs, accurate nailboard documentation, and drive manufacturing automation to succeed. A point often overlooked, the goal to simplify harness manufacturing requires a relentless drive for automation. For one thing, the innumerable options to drive manufacturing automation have made Harness Builder for E3.series a must-have for harness manufacturers. Adding to that, the benefits increase exponentially with the introduction of projection-based augmented reality products like ProjectionWorks by Delta Sigma Company.
Related Content
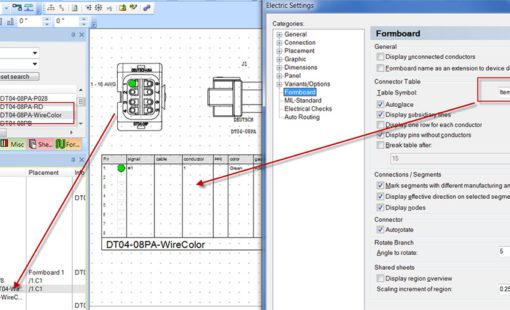
- Products
Harness Builder for E3.series enables wire harness manufacturers to create accurate quotations and comprehensive manufacturing documents, and to drive wire preparation, assembly and testing machines.
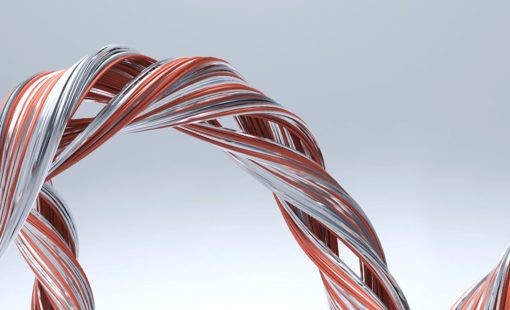
- Products
E3.series is a true concurrent electrical engineering environment supporting advanced requirements for electrical documentation, cabinet and wire harness design and manufacturing outputs.