Systems engineering is an interdisciplinary and integrated approach to designing, building, analyzing, and managing systems. Many manufacturers who adopt it also rely on systems simulation to mimic the operations of different processes through computer models.
A systems simulation, simply defined, is a diagram-based analysis with the inputs and outputs flowing between different system components. Each component is represented by an equation or formula that predicts the performance of some aspect of the overall system. When you put all of these equations together, you end up with a model that can foresee complex behaviors that you might otherwise have missed until prototyping and testing.
Systems simulation offers benefits across many different phases of the product lifecycle, including the development of a systems architecture, the verification of feasibility for design requirements, and the validation of performance across engineering domains.
Exploring Systems Architectures
At its core, engineering is about exploration and iteration. When engineers come to the drawing board, system requirements and their own imaginations are the only limits before them. The more potential design options they can explore—gaining a better understanding of how those different options might perform within a particular system design—the better the result.
Architecture decisions, which are defined early in the development process, have dramatic long-term impact on the success or failure of any given project. So, engineers need to explore and iterate various options for the system, swapping out different components and subsystems as they look to meet design constraints and requirements. The more insights they can glean from different design decisions, the better.
Systems simulation is an excellent tool to address this need. Using systems simulation, engineers can explore and iterate as they make decisions about the underlying foundation of any complex product. They can also learn how the performance of the system as a whole may change with any modifications. Using systems simulation early in the development process helps ensure later project success.
Verifying Requirements Feasibility
Traditionally, systems engineers develop an architecture with key design constraints and requirements and then pass all that information over to detailed design teams. The design team will painstakingly fill in the fine details to ready the design for the next steps in the product development process.
But, as too many engineers have learned the hard way, a particular systems architecture doesn’t always behave the way you think it will. What should work on paper doesn’t always do so in practice. In fact, there are many situations where engineers on design teams try–and fail–to satisfy requirements that were never actually feasible in the first place. Unfortunately, it’s hard to know whether requirements can work in the real world until you’re already well into the design process.
Systems simulation can help. Using such a simulation to verify that requirements are feasible saves the design team significant time and resources upfront and eliminates arduous potential rework. Systems simulation ensures engineers and detailed design teams don’t waste their valuable time pursuing an architecture design that was always doomed to fail.
Validating Performance Across Domains
As the detailed design teams develop each of a system’s subsystem designs, they conduct their own simulations. They may even build out their own prototypes for testing. They do so to verify the subsystem will, in fact, meet requirements and work as intended.
The tricky part is when you combine all the subsystems. There is no guarantee that everything will work as expected when you put the pieces together to create the higher-level system. And too often, this is exactly where organizations run into an excruciating number of prototyping and testing problems.
This stage of design exposes systems-level issues. But more often than not, there is little insight into what is actually causing those complications. To sniff out the root cause, engineers across the different design teams scramble to investigate: Where is the problem, exactly? And how can they solve it without causing an issue with another subsystem or higher-level system as a whole?
Manufacturers can reduce time, costs, and rework at this stage by applying systems simulation. The simulation can progressively verify that each subsystem will perform as designed and expected once plugged into the higher-level system. It is a reliable way to catch issues in the middle or late stages of the development cycle, allowing engineers to easily identify and resolve potential errors before investing in prototyping and testing.
Systems Simulation with Genesys
Today, manufacturers are responsible for designing increasingly complex products. Systems engineering approaches help them manage that complexity across the entire product lifecycle. With Genesys, Zuken offers a powerful tool for defining and simulating systems of any complexity.
Systems simulation with Genesys offers numerous advantages:
- the ability to thoroughly explore and iterate different architecture options at the very beginning of the development process;
- the ability to verify the feasibility of architectures and their various design requirements, and validate the performance of subsystems before prototype and test stages, and;
- more streamlined product design and development that saves valuable time and resources across the product design lifecycle.
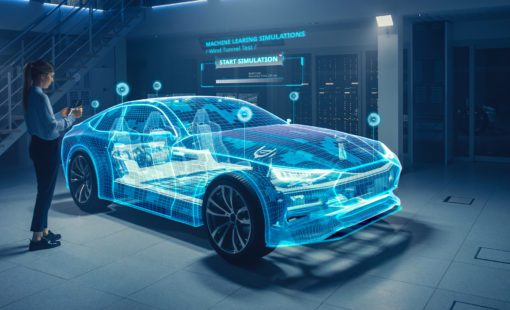
- Webinar
This webinar will discuss the challenges and best practices of creating a MBSE model for the purpose of wire harness and Electronic Control Units (ECU’s) implementation.
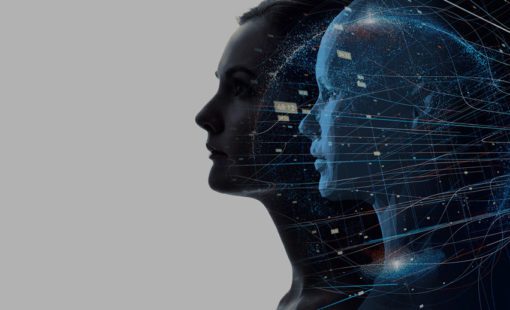
- Solutions
Many companies have recently embarked on the “digital transformation” journey to become more efficient and competitive. A recent IDC study showed that 90% of small and medium-size businesses are budgeting for the digital transformation and 73% have begun the process. .
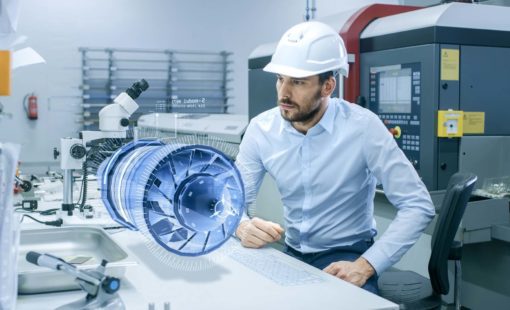
- Products
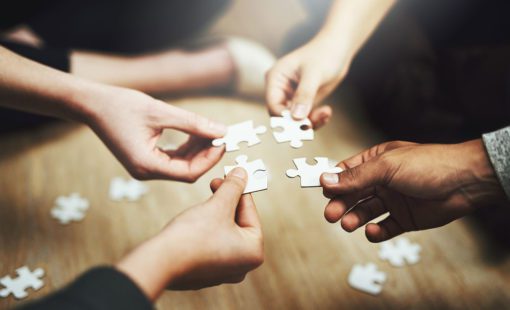
- Webinar
This webinar will discuss the relationship between systems engineering, digital engineering, and MBSE in creating the framework we need to deliver complex products.