Where are electrical manufacturing automation advances taking place?
Electrical manufacturing is a massive industry that demands accuracy and high levels of productivity. To meet these requirements, more manufacturers are moving toward automation and depending more on digital design tools to make that automation possible.
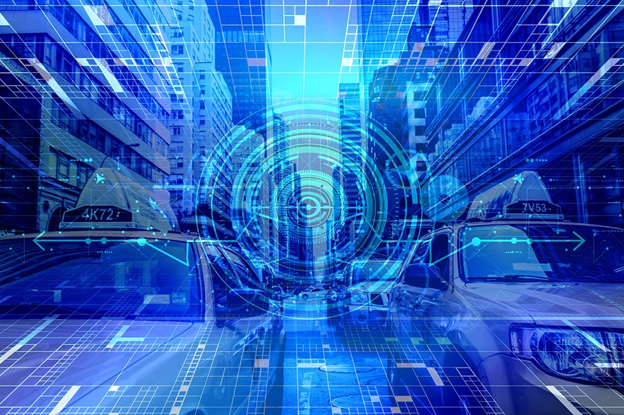
Advances in electrical manufacturing automation technology have yielded automation equipment with higher capacities, better efficiency, more flexibility, and higher productivity. In this blog post, we’ll look at five areas where advances are taking place, along with examples of each.
Interactive Robotics
In general, any time there is improvement in robotics technology, there will be corresponding advances in automation. For example, companies like Fraunhofer IPA are working to develop advanced cabling systems. Their automatic control cabinet cabling system leverages the latest robotic arm technology and motion control to coordinate two arms to work in parallel to place cables. This system also supports the compensation of component and position tolerances, ensuring even force distribution when using very sensitive components.
Another example is the BraiderBot system, a cobot that interacts with humans (hence the term “cobot” rather than “robot”) to braid harnesses. Its robotic arms pull wiring harnesses through the braider, eliminating a time-consuming manufacturing step for technicians. As it performs braiding, the system achieves far more clean and consistent braids than humans; this is made possible by sensors determining the cone angle of the threads. Along with faster harness braiding, the cobot design allows a single operator to run serval machines simultaneously, increasing product yields.
More Efficient Use of Human Labor
One of the issues that arose during the Covid-19 pandemic was a labor shortage due to illness and quarantine requirements. As a result, electrical manufacturing automation experts are developing more complete solutions for processing wires for cabling and harnesses to use labor efficiently.
The Komax Omega 740/750 are wire assembly machines that can produce wiring harnesses (from simple to complex) and include terminal housings on one or both sides of the wiring harness. What sets these machines apart is their ability to include splices in addition to the usual terminals using an ultrasonic splice module. This approach eliminates costly errors that naturally occur when humans are involved, even for simple harnesses like the ones shown in Figure 2.
Flexible Manufacturing for Electrical Applications
Many product manufacturers are moving toward customized products or shorter production runs for some of their products. The processing and assembly of cables and harnesses must be as flexible as with other components in the product; there would be a problematic bottleneck if every other design aspect could be reconfigured within an hour except for the harness.
The Schleuniger Transfer Line Family S50 is an award-winning linear transfer system for processing cables, coaxial cables, and single wires. The operator can quickly reconfigure stations for feeding, coiling, assembly, testing, and other tasks. This technology addresses two of the industry’s urgent requirements: flexible manufacturing and JIT (Just In Time) manufacturing. Both of these requirements help to meet rapidly changing customer needs. Schleuniger offers fully automatic machines and stations for cutting, stripping, crimping, sealing, twisting, and tinning wire–and does so with extremely high precision.
Augmented Reality
Augmented reality has various applications in electrical manufacturing automation, from providing highly informative heads-up displays for maintenance technicians to simplifying the harness manufacturing process. For example, a collaboration between Zuken and Delta Sigma uses augmented reality to eliminate the need for traditional harness boards by projecting the harness layout and assembly instructions onto a blank, reusable board, as shown in Figure 3.
Productivity and harness quality increase because augmented reality harness assembly significantly reduces the probability of error, especially with complex harnesses. This approach also has the added benefit of supporting JIT manufacturing because a simple change in the projection computer allows the user to start immediately on a different harness.
Digital Design Platforms
To effectively take advantage of new advances in electrical manufacturing automation, electrical design must take place in a digital environment that supports manufacturing automation. Designing cables and harnesses requires a different approach for automation, including exporting files in a format compatible with equipment like Komax and Schleuniger.
In electrical harness design, there is Zuken’s E3.series and Harness Builder for E3.series. E3.series supports wire harnesses, control panels, switchgear, and machinery design on one digital platform engineered to support evolving manufacturing and electrical design automation needs. The integrated Harness Builder for E3.series, an example shown in Figure 4, supports pegboard documentation, digital assembly, and communication with wire processing, automated assembly, and testing machines.
Supporting the Future of Electrical Manufacturing Automation
More electrical manufacturers are turning to automation, partly because of its ability to grow and adapt to user needs. Advancements in robotics can lead to new automation features, and wire processing equipment is no exception. Labor shortages during Covid-19 led many manufacturers to re-evaluate how they utilize labor, leading to the adoption of cobots that can work alongside humans to automate harnessing tasks.
The ever-advancing technology behind automated workstations and linear workflows supports the demand for flexible electrical manufacturing. Augmented reality is also finding a niche in harness assembly. And lastly, engineers recognize that digital design platforms are essential to utilize the latest electrical manufacturing automation advances.
Related Products and Resources
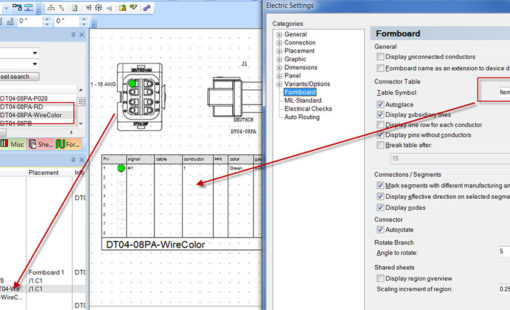
- Products
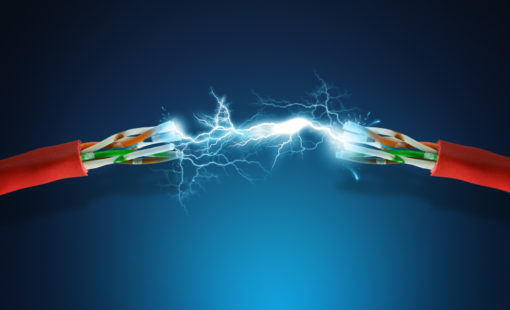
- Products
E3.series is a Windows-based, scalable, easy-to-learn system for the design of wiring and control systems, hydraulics and pneumatics. The out-of-the-box solution includes schematic (for circuit and fluid diagrams), cable (for advanced electrical and fluid design), panel (for cabinet and panel layout), and formboard (for 1:1 wiring harness manufacturing drawings). Integrated with MCAD, E3.series is a complete design engineering solution from concept through physical realization and manufacturing output.