As we witness the birth of an era of connected devices with smart homes, connected cars and smart networked supply chains and factories, we might imagine that unexpected failures of electronic products would be a rarity. But all too often we hear about cellphones going up in flames, airbags that deploy on their own, or drones falling out of the sky. It is estimated that in the automotive industry alone, global warranties amount to as much as $40 billion USD per year.
Whenever things go wrong in a major way, it is a typical reflex to assume somebody made an individual mistake somewhere during an engineering, testing or production task. But investigation often shows that in the majority of cases the disaster is not the result of an individual error, but one that sneaked in somewhere between design and production, when engineers in different disciplines made changes to the original design specification. And it turns out that often a crucial piece of information went unobserved because of poor change management processes. Examples include: a component with a different operating temperature range being used because of a shortage of the originally specified component; or an error in the etching factor of a specific footprint.
Statistical evidence is difficult to find (this is clearly not data any company wants to publish!), but industry insiders are often able to provide plenty of examples whenever the issue comes up, off the record of course.
Best practice for avoiding errors
There are plenty of things a manufacturer can do to avoid these seemingly small errors creeping in and causing mayhem.
- Firstly, start with a consistent component classification system and make sure it is uniform for all manufacturing locations.
- Then make sure the design tools are capable of managing differentiated sets of design rules and net classes to cope with advanced security requirements, such as explosion protection.
- Set up libraries so they conform to the company’s individual manufacturing parameters, such as footprints and etching factors.
- Finally, consolidate material master data and design libraries in a way that they can be directly accessed by engineers and designers whenever they need to make a critical decision.
Endress + Hauser, a global leader in measurement instrumentation, offers a great example of best practice in consistent materials, design library and design data management. The company used Zuken’s DS-2 (now known as DS-CR) to standardize their development and manufacturing processes across several geographically distributed operations. This enabled company-wide parts standardization, design-reuse and increased engineering productivity in a design process for products with elevated operational safety requirements. Their system gives Endress + Hauser the best possible chance of increasing design quality and avoiding those random errors.
Further reading
Success Story: Endress+Hauser standardizes PCB engineering and production processes for industrial measurement products across distributed locations
Related Products and Resources
- Products
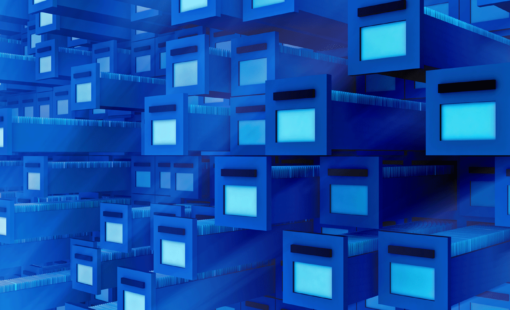
- Products
The traditional practice of mechanical, electrical and electronic engineers working in silos – then consolidating efforts late in the development process – is no longer viable for successful companies. Zuken offers a portfolio of scalable domain data management solutions for PCB and electrical/fluid design plus a range of solutions that integrate design and domain data management into the PLM and ERP world.
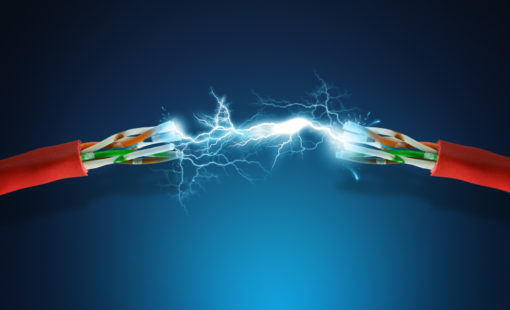
- Products
E3.series is a Windows-based, scalable, easy-to-learn system for the design of wiring and control systems, hydraulics and pneumatics. The out-of-the-box solution includes schematic (for circuit and fluid diagrams), cable (for advanced electrical and fluid design), panel (for cabinet and panel layout), and formboard (for 1:1 wiring harness manufacturing drawings). Integrated with MCAD, E3.series is a complete design engineering solution from concept through physical realization and manufacturing output.
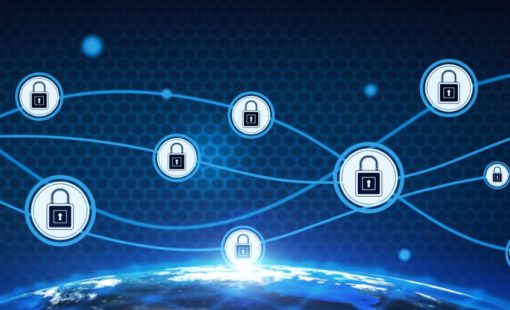
- Products
Zuken’s engineering data management platform DS-CR has been created to support the specific demands of PCB design data management. It combines multi-site library, design data and configuration management into a unified engineering environment.