The industry’s shift toward high-speed designs is evident everywhere. We can see it in motor control units (ECUs), IoT technology, or next-generation wireless communication devices. This shift defines new design challenges for PCB design engineers. In particular, the power distribution system behavior of such a high-speed PCB, its parasitic effects, and the ability to predict its behavior become a severe bottleneck in achieving high operating speeds. Most PCB design flows address these issues to various extents by adding power-integrity analysis and simulation capabilities to the process.
When using complex numerical analysis tools, industrial users face three significant concerns: accuracy, ease of use in the process, and overall performance/computing speed. Any CAD simulation software must overcome these concerns, and so must the solvers in the Zuken PI/EMI analysis environment CR-8000. The 2022 Release includes a new feature that boosts the performance of power integrity analysis through multi-threading technology.
Zuken’s Power Integrity Analysis keeping up with growing PCBs
Zuken’s power integrity solution is remarkably user-friendly in its architecture. It provides power integrity results such as IP-Drop quantities (e.g., current- and voltage-distributions) targeting potential trouble areas directly in the PCB design canvas with just a few clicks. The analysis speed of Zuken’s hybrid solver approach is excellent compared to full-wave 3D-EM simulation approaches for this type of problem. The simulator does not impair analysis accuracy and has a proven history of producing good result correlations1.

The smart hybrid frequency domain solvers employed by the Zuken Power Integrity analysis already outperform most other PI simulation approaches. Yet, users are understandably expecting improvements as boards continue to grow bigger. Some boards may include more than 18 layers, containing multiple power-plane pairs, dozens of power-rails, and thousands of components where the majority often are decoupling capacitors eating up the PCB real estate.
There is a requirement to accelerate simulation performance by using the full processing power of modern multi-core CPUs. Therefore, it was obvious for Zuken’s R&D team to run some of the analysis processes in parallel.
The science behind the new feature
Parallel programming, in general, is a widely used concept with different implementation concepts. It can either describe complete processes ( -> multiprocessing) or only subtasks running distributed and/or parallel on the same machine or even on different machines (in that case, often part of high-performance-computing attempts, HPC). Multi-threading as a mechanism refers to the simultaneous execution of multiple sequential groups of CPU instructions forming a so-called thread. These threads could run on a single processor or even in one of the multiple kernels or cores of modern processors. In fact, it is not actually running instructions in parallel but is permanently switching fast and efficiently between the different tasks by using an intelligent scheduling algorithm.
Intel introduced the hyper-threading (an Intel trademark) technology a couple of years ago, allowing a single processor to operate like two separate virtual processors for the operating system and the applications and programs using it. The physical processor is divided into two logical or virtual processors and improves the performance of the CPU. Hyper-threading technology allows multiple threads to run on each core of a CPU. As IC manufacturers added more and more cores to CPUs, more instructions could be executed simultaneously. The operating system then recognizes each physical core as two virtual (or logical) cores. A single processor can run two threads independently.
Made for parallel processing
The new multi-threaded software architecture of our PI/EMI analysis tool uses the hyper-threading architecture. It separates different analysis tasks into sub-processes and threads, which are then executed, dispatched, and scheduled independently. Because power integrity analysis takes place in the frequency domain, it lends itself quite well to parallel processing since each calculation per frequency can be performed individually by processing the other frequencies of interest.
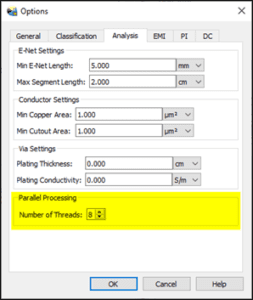
The user can set the number of allowed parallel threads under Options -> Analysis (to leave some CPU resources for other tasks like MS-Office, if desired). This number is limited to the number of the CPU cores or, in the case of a hyper-threading-enabled CPU, to twice the number of the CPU cores. The same applies to AMD’s so-called ‘Simultaneous Multithreading’ equivalent.
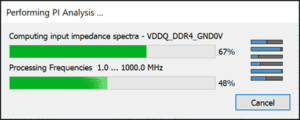
The achievable speed is more or less linear to the number of cores (threads) you free up to be used by the simulator (up to a certain saturation point, of course).
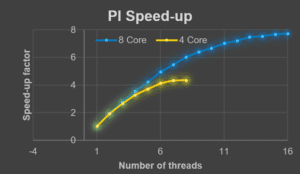
The PDN shown below (a board comprising an Intel Arria © FPGA with 2 DDR4 memories, simulation of the DDR4 core voltage) illustrates the impact on the simulation performance with real numbers. The computing time on my Dell Intel i9 laptop system with 8 cores (32GB main memory, 64bit Windows10) reduces from 3 minutes down to 20 sec with all threads activated. This defines a serious improvement in the analysis efficiency, especially when evaluating different design alternatives for the PDN structure.
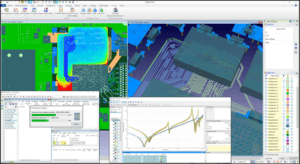
Summary
CR-8000 includes fully integrated signal integrity and power integrity analysis and simulation tools to verify all aspects of your single or multi-board PCB designs. Learn more on our website.
—
References:
[1] Brüning, Ralf, Kakerow, Ralf, Wagner, Torsten.; ” A Multistage ‘Power Integrity Surgery’ for the Design of Complex Automotive Electronic Control Units”, IEEE EMC&SI Symposium 2015, Santa Clara, CA, USA March 2015
Related Products and Resources
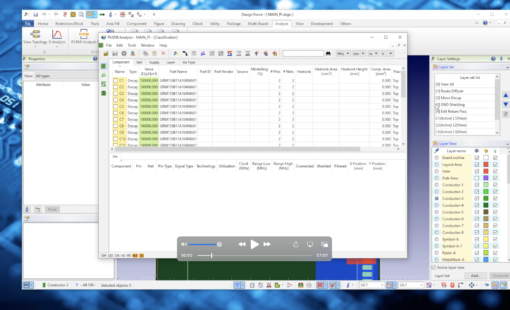
- Blog
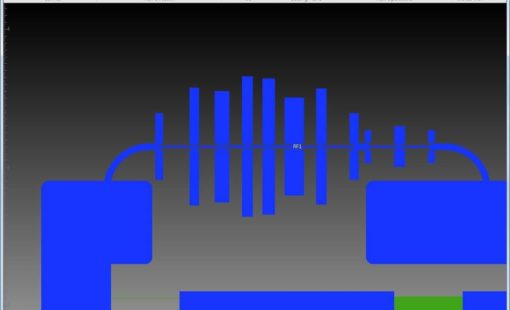
- Products
For a complete RF verification flow, CR-8000 Design Force interfaces with best-in-class, high-speed RF and electromagnetic analysis solutions.
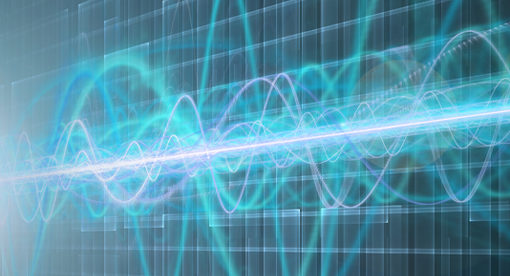
- Webinar
The fast signal switching times of today’s digital systems require particular attention to the signal integrity during design to ensure reliable operation and EMI control.
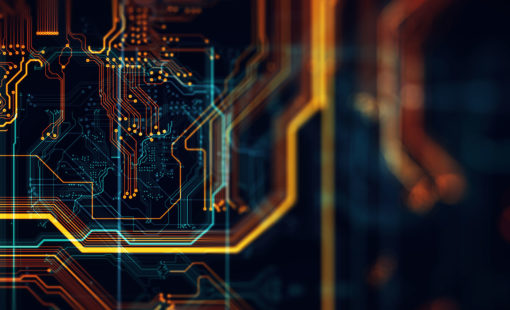
- Products
Building a competitive product today is much more difficult than a few years ago. Existing PCB-centric design processes are limited to a single PCB and do not provide the necessary tools for today’s competitive product development environment. PCB-centric design processes are falling behind.