There are many challenges on the road to achieving digital transformation and connecting systems engineering to detailed design. The two biggest challenges are ‘too much Information’ and ‘too little Information’. Therefore, a simple answer is a balanced approach, addressing both sides of the equation. Unfortunately, it is difficult to have a common set of rules for various product types. Not only that, the myriad of teams, business processes, and requirements is challenging to manage. Moreover, balancing system complexity while fine-tuning for an appropriate level of detail is extremely challenging. Suffice to say, success depends on the emergence of a cogent process to achieve balance.
At Zuken, we are working with an effective mix of industry leaders, early adopters, and experts to address the biggest challenges of digital transformation. The E3.GENESYS Connector is our latest solution to keep the systems engineering product model relevant in the detailed design process.
Capturing Design Details in the System Engineering Model
The history of a product plays an outsized role in determining the best practices for successfully connecting systems engineering to detailed design. For instance, in new product development, many of the components are unlikely to have part numbers. Signals, pins, and connectivity details are in flux as a product matures through the development cycles. Therefore, it is important to capture relevant information such as nets and functional connectivity and transfer that to detailed design. Conversely, in an iterative product, the components, signals, pins, and connectivity are more established. There is a greater incentive to utilize as much of the previous design. Moreover, using tried and tested parts of the previous iteration reduces the chances of unforeseen failures.
The nuances of the product development might differ across teams. Establishing a few ground rules helps teams simultaneously work on new products as well as iterative products. For instance, a rule barring wires and pin-to-pin connectivity details from the systems engineering product model keeps the model simple. Simultaneously providing a way to document a connector or a reuse block is imperative to drive detailed design.
E3.GENESYS Connector
E3.GENESYS Connector creates a ground-breaking process to connect the E3.series project directly to the systems engineering model. The connection process consists of three steps. Firstly, create a direct secure connection to the Vitech GENESYS server on a local or remote server. Secondly, select the desired project and the appropriate sub-system to connect with the E3.series project. Finally, create a new link by importing the sub-system layout or re-establish an existing link. E3.GENESYS Connector is built around the principle that GENESYS is the one true source of the product model. Therefore, without leaving E3.series or learning the GENESYS tool, the electrical designer can review the various representations of the system metamodel to better understand the system scope.
This link between the E3.series project and the GENESYS model is beneficial to the entire design process at many levels. Firstly, the application transfers all the relevant systems to the E3.series project. To avoid rework, the application replicates the GENESYS system layout in a high-level topology drawing. Secondly, the assignment of connections, links, and nets to the appropriate blocks establishes logical connectivity. The nets from the systems model transform into signals in E3.series to establish signal flow across multiple systems throughout the project. Thirdly, the system maps the component attributes, parameters, and requirements to the appropriate blocks in E3.series. Consequently, there is no duplication of effort, and all the relevant information from the model is available in the E3.series project. Most importantly, the key element to success is balancing the extension of the systems model to include the right information for detailed design and reimagining the design flow in detailed design.
Model-Based Systems Engineering to Detailed Design
For a more in-depth look, join our webinar detailing the GENESYS to E3.series design process using the E3.GENESYS Connector.
Digital Engineering Basics – MBSE to Wire Harness Design (Part 3)
This webinar is part of the the ‘Digital Engineering Basics’ series that explores the digital engineering process. We will explore everything right from building the model to verifying model requirements, trade-off analysis, and moving the model into the detailed design for wire harness design.
Detailed Design to Manufacturing
The benefits of keeping the systems model relevant in detailed design are far-reaching. The connectivity to E3.series automatically makes the model relevant even in the manufacturing realm. The always up-to-date nature of the E3.series project and its ability to create connected representative views of data greatly impact the design cycle. For instance, Harness Builder for E3.series can transform the data from the product model into detailed manufacturing-ready information. The built-in options drive automated testing, wire processing, labeling, and other automated manufacturing options. Similarly, the intelligent cabinet design automation options in E3.panel transform logical connectivity into 2D data and 3D layout data to drive manufacturing.
Conclusion
A seamless connection between different stages of product development is the best way to fully realize the benefits of digital engineering. A successful connection between systems engineering and detailed design provides a huge boost in productivity. Furthermore, it also unlocks greats competitive advantages in the quality and usability of the end product.
E3.GENESYS Connector gives an E3.series user full access to the Vitech GENESYS model in terms of project selection, diagrams, requirements, and parameters. It is an optimal solution to eliminate the tedious process of translating the system model to a set of documents, only to transfer and redo the work in detailed design.
It is an exciting time to be in pursuit of digital transformation. The technologies and processes are accelerating at a remarkable rate, putting success within reach. Zuken understands the gaps and is actively delivering toolchains and expertise to bridge the gaps. Read more at zuken.com/us/solution/digital-engineering/
Related Products & Resources
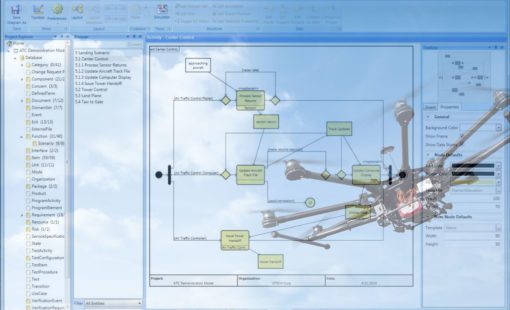
- White Paper
This eBook describes an MBSE based process for Electrical and Electronic design. The eBook begins with model content and structure with the purpose of implementation and the need for a “design envelope”.
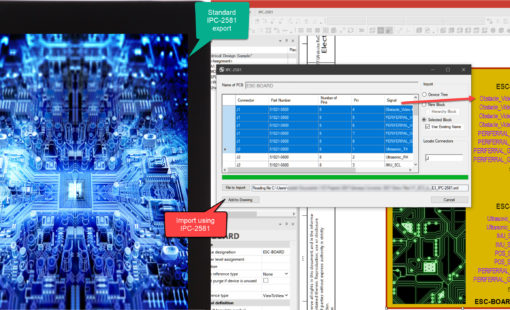
- Products
Digital Engineering requires a model-based design process that begins in Systems Engineering. Zuken acquired Vitech Corporation, a leader in Systems Engineering practices and MBSE solutions, with the intent of implementing an E/E model-based design process.
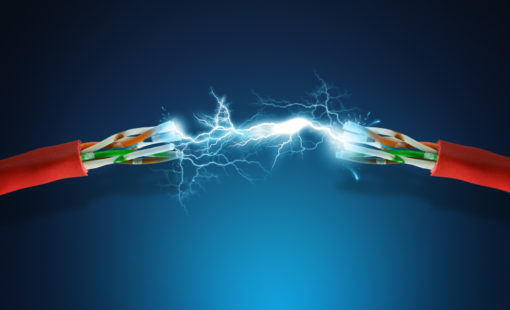
- Products
E3.series is a Windows-based, scalable, easy-to-learn system for the design of wiring and control systems, hydraulics and pneumatics. The out-of-the-box solution includes schematic (for circuit and fluid diagrams), cable (for advanced electrical and fluid design), panel (for cabinet and panel layout), and formboard (for 1:1 wiring harness manufacturing drawings). Integrated with MCAD, E3.series is a complete design engineering solution from concept through physical realization and manufacturing output.