An immature design or manufacturing process invariably leads to excess complexity. In some cases, complexity is good, but manufacturing is not one of those cases. The manufacturing process is complex because it has evolved over time. Evolution in principle is an eventuality and not a grand plan. These complex and manual processes need a holistic overhaul to gain efficiency and see savings. Smart manufacturing options driven by intelligent design solutions provide a repeatable and efficient path to simplify manufacturing processes.
Breaking down complexity means utilizing simple and efficient methods to drive multiple processes. In simple terms; If we know the reason for inefficiencies in the process, then we must remedy it. The reality, as you know, is not that straight-forward. Firstly, clichéd as it may sound, the most common roadblock for improvement is the fear of change. Secondly, robust thought leadership is necessary for an optimal solution. Thirdly, and most importantly, the solution must address the core challenges, not only the superficial annoyances.
Today, many cutting-edge industrial solutions provide varying levels of automation. Moreover, the mass-market adoption of automation solutions is rising quickly across all industries. Most notably, the fastest growth is in the power, control panel, and harness manufacturing industries. All machines need intelligent design data to unlock their smart manufacturing potential. E3.series provides direct and indirect paths to connect with various automated manufacturing options. The E3.series design suite along with strategic industry partnerships is paving the path to success. This post explores the preliminary options available to start the journey towards smart manufacturing.
Automating Wire Processing
At Zuken, we believe in building partnerships to rapidly expand the entire design-to-manufacturing ecosystem. Zuken, across various platforms, supports automated wire processing machines to simplify and increase manufacturing throughput. The outdated and yet standard practice for wiring consists of all or most of the following steps:
- Identify the connection origin and destination
- Choose the correct wire size
- Find the appropriate tools
- Strip and terminate one end of the wire
- Cut the wire to the desired length i.e., measure or guess the required length
- Strip and terminate the other end of the wire
- Repeat for the next wire
Automated wire processing machines vary in their levels of automation. However, most commonly, 50% of the above tasks can potentially be automated.
Additionally, In E3.series, wires route intelligently in the 3D panel, or the formboard meticulously details the length. Most importantly, leading automated wire processing machines read and process wires directly from E3.series. For instance, the E3.panel drives cutting-edge machines such as the Komax Zeta series. Komax machines bundle and mark the wires based on the optimal sequence of wires in a design driven by standard parameters. As a result, the potential time-savings are greater than fifty percent. Furthermore, research suggests that wire assembly can quickly come down to 2-3mins per wire, or even less.
Automated Cutting and Assembly Options
CNC machines and other automated cutting machines are not new by any means. To be precise, they are the defacto standard across manufacturing floors. Even so, the fabrication of a control panel is a challenging task for automation. The cut-outs and drill-holes are driven by the parts placed in the panel. Furthermore, layouts vary between din rail-mounted or direct-mounted items. Thus, the possible combinations are large enough to make standardization the key challenge.
E3.series provides robust tools to create panel design in 3D and 2D. So, the design is complete with details for mechanical fit and finish. As a result, automated machines can speed up the manufacturing readiness targets. E3.cutout is an add-on tool available with E3.panel. In addition, tools to drive labels, cable protection, and other peripherals can be driven from the information captured in the design process. Similarly, the formboard layout can drive the automated creation of harnesses with advanced wiring machines.
Augmented Digital Assembly
The goal of every person responsible for improving manufacturing efficiency must be to reduce non-value-added tasks. Time spent on tasks such as looking up information for assembly can instead be time available for improving efficiencies. The challenge is to settle on the right amount of data required to maintain the balance between manufacturing efficiency and increasing complexity.
A simple path forward is to utilize products such as ProjectionWorks from Delta Sigma Company. ProjectionWorks uses step-by-step harness manufacturing information exported from E3.series delivered using a unique augmented reality projection system. To learn more, sign-up for our webinar with Delta-Sigma.
Digital Delivery to Drive Smart Manufacturing
The information available for full augmented reality solutions is limited to specific applications. To simplify the process, E3.series add-ons provide the digital wiring and quality control and tracking options to ease into the smart manufacturing options. Two main add-ons assist with digital delivery and tracking. First, E3.WiringCockpit provides simple wire-by-wire information to the assembly technician. Second, E3.WiringChecks provides a robust error checking and capture tool. The checking process provides an elevated change and error tracking opportunity. To learn more about these digital engineering-to-manufacturing solutions tune in to our on-demand webinar.
E3.series and Smart Manufacturing
The electrical design world is a strange place with drastic differences from one company to the next. On the one hand, many teams are simplifying and automating processes at every stage. On the other hand, teams are forming the last bastions of archaic design practices. A lot of it comes down to the end customer and their requirements. If the term “don’t fix what’s not broken” comes up often, improvements are less common. Maintaining the status quo makes for smooth sailing, but only for a short period of time. We believe in moving forward with cutting-edge innovation, continuous improvement, and robust partnerships.
Around the globe, Zuken is working with manufacturers, partners, and customers to improve design-to-manufacturing automation. There are many exciting developments with new partners and new possibilities for further improving the efficiency and efficacy of digital design. Stay tuned and watch this space as we discuss design solutions, partnerships, and all the exciting updates about smart manufacturing.
Related Products and Resources
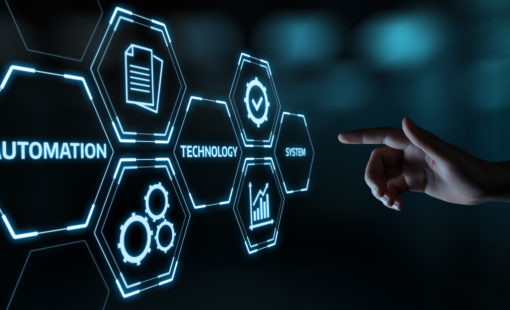
- Webinar
This webinar will introduce the new functionality in E3.series 2020 and summarize some of the more important existing functions in this industry-leading design solution.
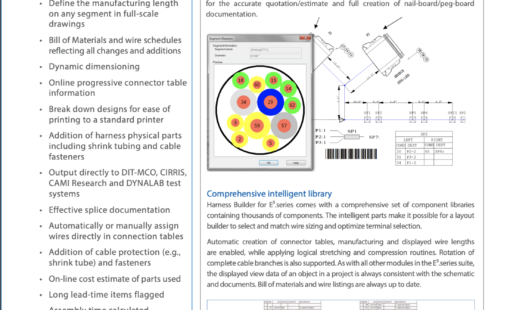