This blog post is for those new to electromagnetic compatibility. I’m not about to get into the physics of electromagnetic theory, but jump straight to the electronics design challenges and then move on to provide tips that you can get on with straight away to overcome these. If you do want to find out more about the physical interaction between the electrically charged particles that is known as electromagnetism, Wikipedia does a sufficient job of explaining it.
You’ll already be well aware that EMC compliance is a necessary condition for releasing products to market. There’s National and International bodies such as the IEC and the FCC that define limits on how much a device is allowed to produce, and the how stringent these are will vary according to industry.
Definitions
While I’m not going to indulge you in the world of physics, some basic definitions are essential before we move on.
-
Electro-Magnetic Compatibility (EMC) is the ability of a product to function in its environment without introducing electromagnetic disturbance. So the product must:
- Tolerate a specified degree of interference.
- Not generate more than a specified amount of interference.
- Be self-compatible.
EMC is the control of EMI described below,
- Electromagnetic interference (EMI) is disturbance that affects an electrical circuit due to either electromagnetic induction or electromagnetic radiation.
- Electromagnetic noise is the interference we are talking about above, which is produced as a result of rapid current and voltage changes.
EMC Design Challenges
We don’t need to talk about the electromagnetic spectrum to appreciate that the difficulties surrounding EMC stem from two areas:
- Emissions
Here I’m talking about the unwanted energy created by components or traces that can interfere with other components and traces etc. The designer is focused on minimizing or blocking this. They might be just getting on and doing their business, but think of all the components that they are messing with around them?
- Susceptibility
This is the component or trace which is the victim of the unwanted energy (noise) from the emission releaser above. This is the regular component just doing its job, them wham, they are bombarded with electromagnetic interference that causes all kinds of havoc. The designer might want to move these components or find ways of toughening them up so they aren’t affected.
The upshot here to ensuring compatibility is about addressing both the (selfish) emission releasers and the (unsuspecting) victim of the releases. Think of someone playing loud music on a train, you can get them to turn their music down so it is not being so intrusive (‘hey man, can you turn it down please?’) you can get used to the loud music (OK so this track is not so bad), or maybe you can wear ear plugs or ear defenders (I will NOT let this awful music ruin my commute this morning).
Four Steps to Ensure Acceptable EMC
We all like a set of easy steps don’t we? Here’s four to get you started on EMC heaven.
- Characterize the threats – understand what the potential is.
- Review the standards for emission and susceptibility levels – how does the threat apply within these?
- Design for compliance – make sure you keep compliance requirements in mind throughout the design process.
- Analyze and test for compliance – use your design tool prior to fabrication. Make sure it can:
- Perform appropriate rule checks for critical wiring and parts.
- Ensure rule checks are well documented (explain and advise on correction).
- Support thresholds and allow weightings.
- Allow both quick analysis and in-depth analysis.
EMC Quick Design Tips
Now let’s get to the technical detail, here’s some tips to start implementing straight away.
- Place decoupling capacitors as close to the power pins of IC’s as possible. If you’re wiring rather than using vias, make sure the wiring is as short as possible.
- With clock wiring, keep as short as possible to avoid potential antenna.
- Eliminate isolated copper areas to avoid potential antennas. Connect any isolated copper areas to ground.
- When you are working with power and ground nets, minimize the loop areas as they can act as receiving antenna for external noise.
- Monitor the proximity of wiring which can easily generate noise to wiring to those that can easily receive noise. Insufficient clearance can result in “crosstalk” (when one signal creates an undesired effect on another signal).
Watch the Webinar
Want to move onto the next level? Watch my webinar titled Electromagnetic Compatibility (EMC) Design Basics to learn more tips and for a demo on EMC Adviser EX, in Zuken’s CR-8000 Design Force design software which:
- Reviews the EMC checks available.
- Analyzes several designs for EMC issues.
- Proper ground shielding around a clock net.
- Proper return path for high-speed signals.
- Proper distance between active and passive traces to avoid crosstalk.
- Shows the adjustment to routing and re-run of analysis to verify that potential EMC issues have been resolved.
Access Webinar
Q&A
Have some questions? Check out the Q&As below or feel free to drop me an email at craig.armenti@zukenusa.com
Don’t just focus on EMI, also work on EMC – why?
The impact can be much greater and more cost effective.
How many EMC analysis cycles should I be doing?
At least one cycle, but better still one during the design and one at the end of the design. Don’t wait till fabrication to fail compliance, because it costs you so much more to rectify. Many design teams focus on the EMI and forget about EMC prior to fab.
Related Products and Resources
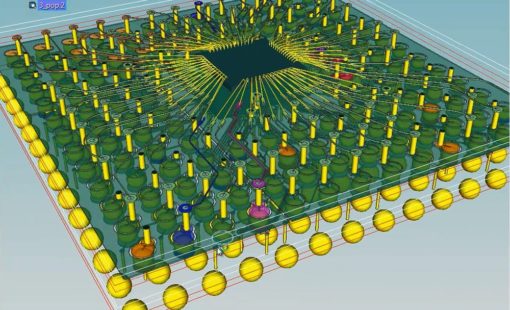
- Products
Design Force offers an intuitive, integrated environment for designing single and multi-die packages for wire-bond, flip-chip, and high density advanced packaging. Designers can start designs with early prototype input of chip and package data from the library, reuse data from IC layout tools, and take advantage of parametric wizards to streamline the creation of the system
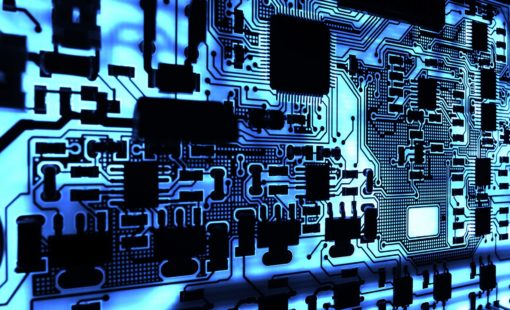
- Products
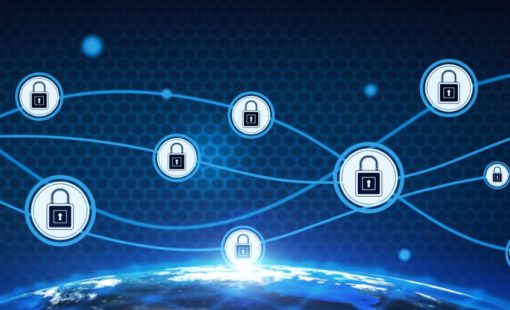
- Products
Zuken’s engineering data management platform DS-CR has been created to support the specific demands of PCB design data management. It combines multi-site library, design data and configuration management into a unified engineering environment.
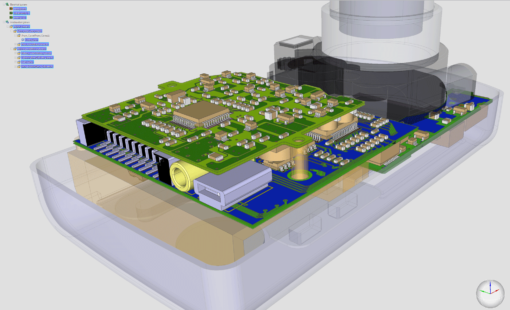
- Products
Design Force combines traditional 2D design with native 3D design and the latest human interface techniques, accelerated graphics and almost instantaneous rendering and refreshing. It is the fastest, most effective PCB design solution available today. Design Force enables design teams to layout their designs in the context of a complete system or product.