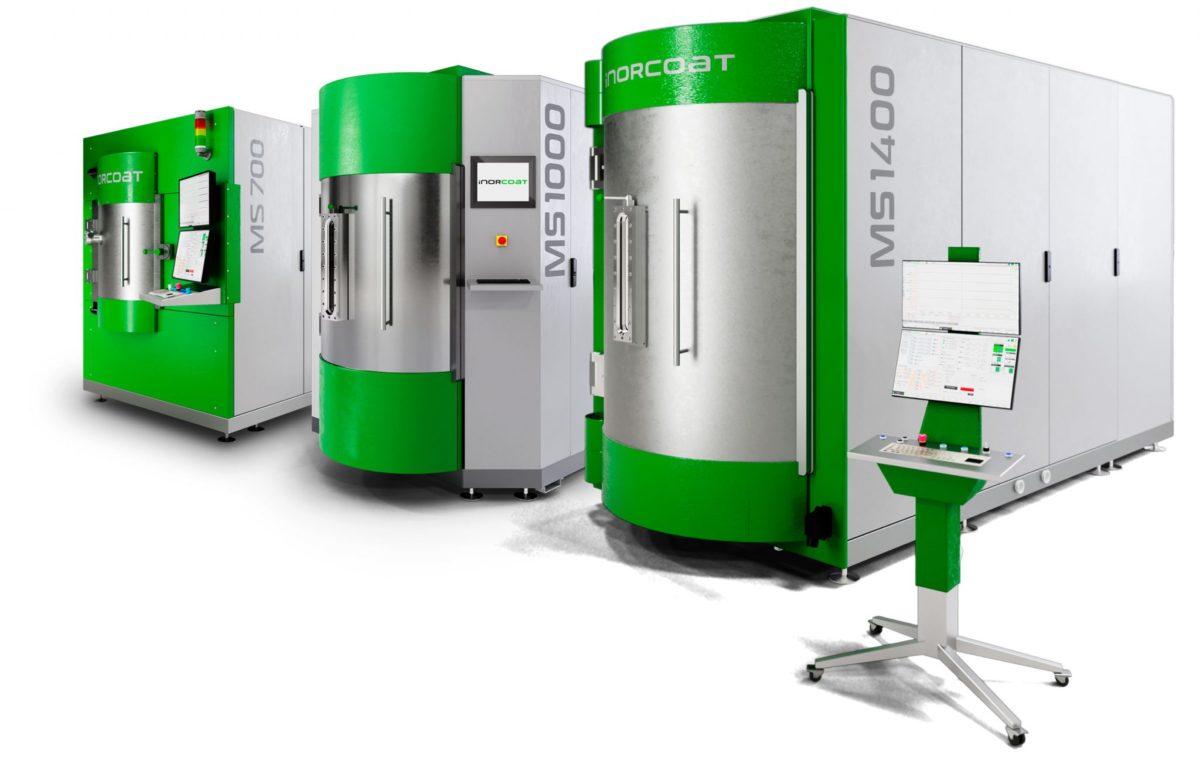
The start-up company, INORCOAT, relies on Zuken’s E3.series for the development of environmentally friendly nanotechnology coating systems. The first system was recently put into operation at the Portuguese National Bank to coat dies for euro coins. However, the possible applications go far beyond dies and printing plates. E3.series offers the possibility of reliably adapting the electrotechnical equipment of the plants to specific areas of application and configurations.
Environmentally friendly technologies are in high demand these days–reduction of CO2 emissions, avoidance of environmental toxins, and conservation of natural resources are just some of the keywords we are hearing in the media almost every day. Unfortunately, environmental sustainability comes at a price. In many cases, alternative technologies are available. Still, many of them continue to be too expensive to replace fully–or to substitute–established processes that are becoming increasingly questionable from an environmental point of view.
A good example of environmentally harmful technologies is galvanic chrome plating–a process that is not only used to add luster to Daddy’s Harley but also to increase resistance to wear in industrial applications: cylinder liners of combustion engines, for example, are galvanically chrome plated. In mechanical engineering, the process is used to finish casings, pistons, molds, and gauging tools, and even in the food industry, pipes, cooling and drying cylinders as well as screws are hard chrome plated.
We looked at the available systems and examined them from this perspective: Is there any way to make things simpler and better without compromising the quality of the result in the long term?
However, galvanic chrome plating has a serious disadvantage: it is highly harmful to the environment and should have been banned in the EU already in 2017. This deadline was extended until 2024, probably in no small part due to the lack of availability of an economical substitute technology. Still, sooner or later, it will have to be replaced by alternative processes. These are, in fact, available with plasma coating technology – also known as PVD (physical vapor deposition) in technical jargon – but they are currently too expensive and inefficient for many industrial applications.
Making environmentally friendly substitution technologies economically viable
It was this shortcoming that Romain Waidelich set out to remedy with his start-up company INORCOAT. His vision is “to simplify the complex plasma coating or PVD process and make it more understandable and accessible to the customer.”
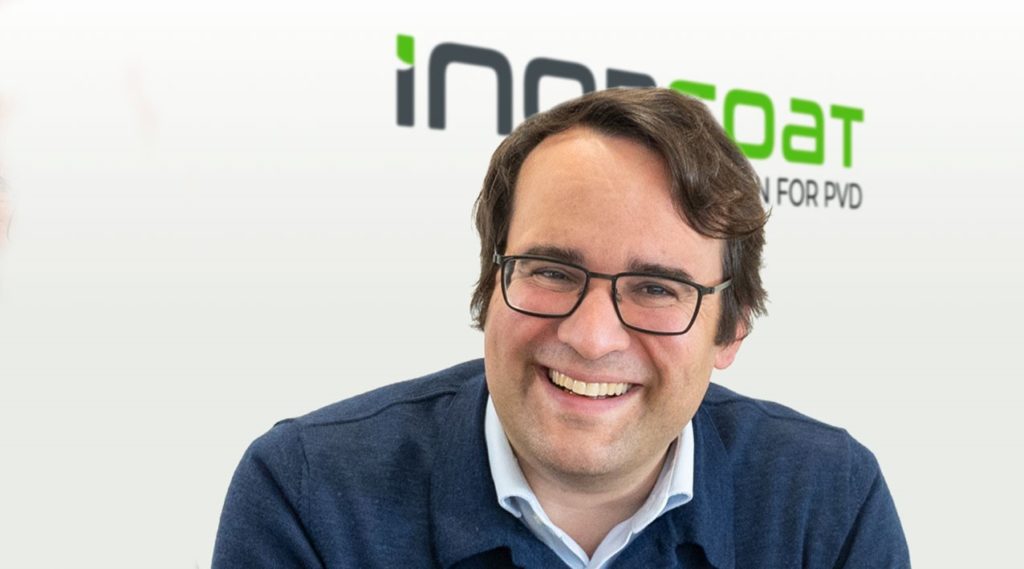
As a process engineer with many years of experience in the process industry (pharmaceuticals, food) and the automotive supply sector, Romain Waidelich has been involved with PVD technology as an alternative to electroplating for many years. Out of this long-standing involvement, he concluded that the technology could benefit from a fresh approach: “Many commercially available systems were developed primarily from a scientific point of view and are therefore often very expensive for an industrial kind of deployment.”
In other words, through consistent optimization, it ought to be possible to significantly reduce the cost of PVD coating processes. “We looked at the available equipment and analyzed it under the aspects of: Could it be done easier and better without compromising the quality of the result in the long term? We concluded that with a consistent approach to implementation, a savings potential of up to 50% could be achieved”, Romain Waidelich reveals.
Market entry through the minting process of coins
This idea led Romain Waidelich to become a self-employed entrepreneur in 2019 and to the founding of the company INORCOAT in 2020. As part of a public call for tenders issued by the Portuguese National Mint and Printing Institute INCM, a PVD coating machine was developed for the minting dies of Portuguese Euro coins.
The reason for this not immediately apparent cooperation is quickly found: coins have to be produced in large quantities in consistent quality with high demands on detailing and design. To reduce wear, the dies are therefore hard-chrome plated – in the past by electroplating and in the future by a PVD process with innovative coatings. New 1-euro coins and medals minted in Portugal are already being produced with the help of PVD technology from INORCOAT.
Today, INORCOAT offers four basic configurations with the MS 700, MS 1000, MS 1400, and MS 2000 product series, produced in an elaborate design that matches the sophistication of their technology. Each of these four types can be individually configured and adapted to customer-specific requirements because the field of application for INORCOAT machines is by no means limited to coin embossing dies or printing plates for central banks, where the focus is on hardness and wear resistance, but also for a wide range of industrial applications.
Reliable data for the supply chain
To create the data for the electrical design of the PVD systems, INORCOAT relies on Zuken’s E3.series. “The electronic and electrotechnical systems are, in a way, the heart of a PVD system,” says company owner Romain Waidelich. “We are working in the range of 100 kW and therefore have to meet stringent requirements for EMC certification. Comprehensive and reliable documentation. Comprehensive and reliable documentation such as E3.series provides us is therefore very important.”
Another critical aspect is cost containment and quality management: “As a lean organization, we rely on a flexible cooperation with suppliers,” explains Romain Waidelich. “We, therefore, find it important to keep control cabinet and cabling development in-house as a core competence. With E3.series, we have the capability to configure our systems in a modular approach from a library of certified components and to produce accurate data for quotation and commissioning at the push of a button.”
In this way, the company sees itself well equipped to explore new applications in the process industry, mechanical engineering, and aviation. Even design options such as the use of color – even on coins – are feasible. The cooperation with the Portuguese National Bank has apparently got “the coin” rolling. It will be interesting to see what happens next.