This is the second and final, in my series of posts that look at aspects of dealing with change in the aerospace industry. There is also a webinar to support this available to download on-demand and a YouTube preview to watch at the end of this post.
Last time I talked about the impact of failure and the process of detecting it, today I’m going to focus on resolving it.
Failure resolution through change – the easy way
Accepting failure in parts of the product development process and implementing a design process that allows you to easily and efficiently overcome these is critical. If a design failure occurs in a component used in a large project, the time to search every instance and update it with a new component can be very significant.
It definitely pays to have a design documentation structure that allows you to capture all instances of a given component and update them all at once – like that offered by our electrical E-CAD software E³.series.
In a large and complex project there will inevitably be large amounts of documentation in the form of design schematics, test and validation procedures and results. A failure anywhere in the design or process will involve all departments involved with the product or project; in effect the whole manufacturing process would have to start all over again.
You need to be able to manage this change in an effective and efficient way. If one single component failure has been detected, how do you know where else in the design that component is also used? Maybe that component is part of an assembly and the design elements could be placed on many sheets in the design. You should not have to search through hundreds of components or hundreds of sheets to find the component occurrences. You need a design tool that is object oriented, so the tool can easily identify the component by its class, attributes, or data model – like E³.series.
Any change made anywhere in the design will be then occur on every instance throughout the design – now that’s time saving on a big scale.
Tracing failures throughout all versions and revisions
If the change is made, how do you know where these have taken place? There can be many occurrences of a failed component. If the change is complex, even with the best will in the world, some changes could be lost, should you be under pressure to implement the modifications to the design as quickly as possible. So you need a revision management tool that can track the changes as they occur, and when finished and issued, be able to reproduce the changes in a textual, graphical and tabular form for quality assurance purposes – this will enable accurate, and efficient documentation of the change.
The problem may become more complex if the change happens where there are variations or options on the product – you now need an efficient option and variant capability within the tool, meaning that any variation or option to the design can be selected or de-selected during the design process or indeed during the change process.
During the on-demand version of the webinar on this topic, I’ll be showing you have to identify, and resolve failures within the design environment, using E³.series to illustrate my points. Why not go and check it out? Below is a preview of this webinar:
- Read the previous post Save Time and Reduce Risk By Managing Change in Complex Electrical Aerospace Projects to Overcome Failure (Part 1)
- Find out more about the other aerospace electrical design webinars available on-demand
Related Products and Resources
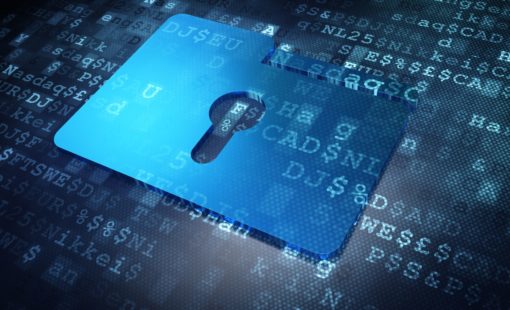
- Products
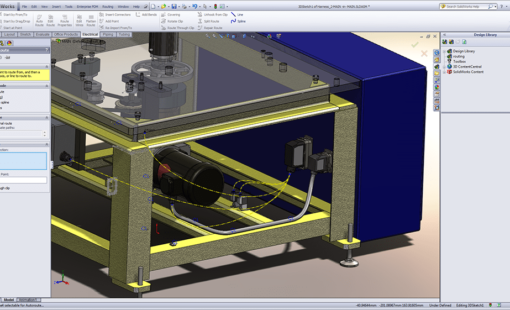
- Products
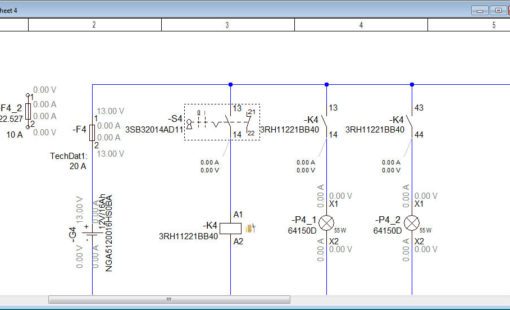
- Products
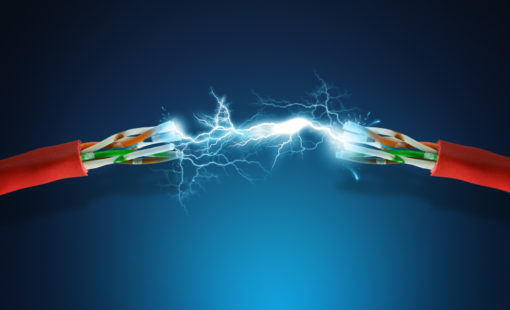
- Products
E3.series is a Windows-based, scalable, easy-to-learn system for the design of wiring and control systems, hydraulics and pneumatics. The out-of-the-box solution includes schematic (for circuit and fluid diagrams), cable (for advanced electrical and fluid design), panel (for cabinet and panel layout), and formboard (for 1:1 wiring harness manufacturing drawings). Integrated with MCAD, E3.series is a complete design engineering solution from concept through physical realization and manufacturing output.