The embarrassment of choice has become a powerful sales instrument – not only in the consumer market, where an abundance of sizes, colors, styles and flavors tempts the buyer to load more items into their shopping cart than they have on their shopping list.
It is also a powerful differentiator the investment goods industry. Bespoke products that are customized to meet a customer’s business needs are an important driver for companies that operate at the high end of their respective markets, such as automation, industrial machinery and transportation.
No such thing as choice without implications
But diversity doesn’t just provide new business opportunities – it also comes with a number of implications, such as additional costs in engineering, sourcing and manufacturing that threaten to eat up margins and profitability. The reasons for these collateral effects can be easily summarized as “complexity”. More variants call for more bespoke engineering, bespoke engineering calls for more custom parts to be ordered from the supply chain, and so on. The result is growing complexity in project management and production. And, last, but not least, the assembled products have to be tested to make sure the final product is able to live up to its high-end quality promise.
How do you take the complex out of complexity?
It is no surprise that manufacturing companies are looking for ways to bridge the gap between customized products and standardization. And it is a logical next step to think about IT-based configuration tools that help configure a product from a set of off-the-shelf building blocks that can be combined without the downside of runaway costs.
Unfortunately, there is no such thing as a standard remedy – and there is no such thing as a bespoke product built only from off-the-shelf components: as much as every manufacturing company considers itself unique, there are also unique approaches to simplification. These need to be investigated and developed before any important IT investment decisions can be made.
To help decision makers through the often complex process of establishing their unique approach to simplification, we have researched and compiled an overview of proven methods and instruments that have been developed and applied over the past two decades. We will discuss our findings in the upcoming Webinar. “Get your complexity under control: An introduction to handling product and variant diversity, and approaching electromechanical data management with confidence.”
Live Webinar
The webinar provides an overview of complexity drivers and containment approaches, and offers a practical, introductory guideline to managing complexity. We will also look at challenges posed by electromechanical engineering and managing data as part of the product development process.
What you’ll learn:
- Who needs to be involved with product variety
- Feature versus variant – what’s the difference?
- How to deal with business challenges thrown up by product complexity
- How to handle product variety
- The next level: digital networking of products and services
- How to provide relevant information
Sign up now to the webinar:
Subject: “Get your complexity under control: An introduction to handling product and variant diversity, and approaching electromechanical data management with confidence.”
Date:
Related Products and Resources
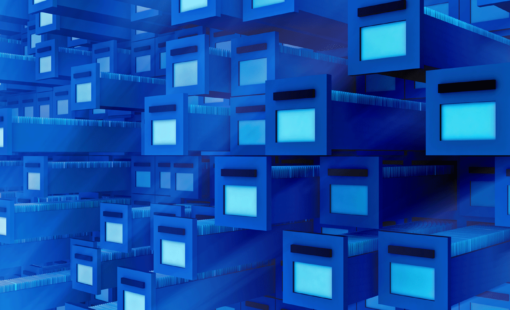
- Products
The traditional practice of mechanical, electrical and electronic engineers working in silos – then consolidating efforts late in the development process – is no longer viable for successful companies. Zuken offers a portfolio of scalable domain data management solutions for PCB and electrical/fluid design plus a range of solutions that integrate design and domain data management into the PLM and ERP world.
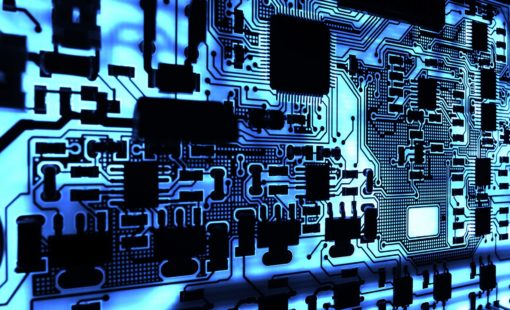
- Products
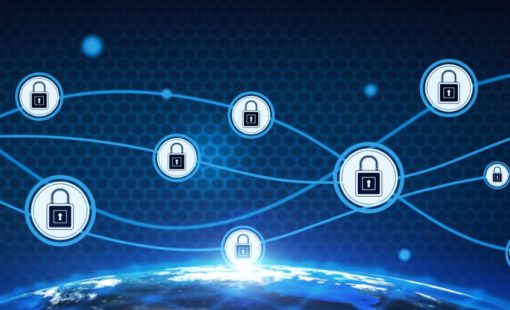
- Products
Zuken’s engineering data management platform DS-CR has been created to support the specific demands of PCB design data management. It combines multi-site library, design data and configuration management into a unified engineering environment.
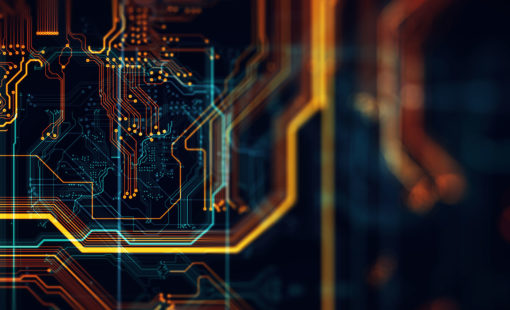
- Products
Building a competitive product today is much more difficult than a few years ago. Existing PCB-centric design processes are limited to a single PCB and do not provide the necessary tools for today’s competitive product development environment. PCB-centric design processes are falling behind.