I’m back once more to share with you my final blog post on DAMA – Design Anywhere, Manufacture Anywhere – and its impact on Electronics design.
This time I want to talk to you more about the realities of implementing this approach starting with the initial audit process and understanding the real payback.
Creating a DAMA capable enterprise
1) The importance of a detailed audit
No one said auditing was fun, but there is no playing dodgeball on this one. It’s really important to gain a deep understanding of the structure and organization of the current enterprise and this doesn’t mean sitting back and delving around in your IT structures. I’m talking here about interviewing engineers, purchasing staff, manufacturing managers, and general management. Yes, that’s correct, actually talking to them.
2) Mapping capabilities to create a gap analysis
This involves mapping the organization’s capabilities against best-practice objectives to perform a gap analysis for each category analyzed. What I’m saying is, compare what you’re doing and what you’re capable of doing against what you should be doing and see where the gap is – simple…um no, but it sounds it doesn’t it?
To make it really hold weight, the categories you are reviewing should be weighted so that you understand the systems and processes that have the greatest impact on the business – and these are then reflected in your conclusions.
In Zuken’s experience, 60%-65% of DAMA-related problems at customer sites can be resolved by harmonizing business processes, whereas less than 5% can be addressed by tackling issues related to the CAD environment in isolation. Even at the overall IT level, only 30%-35% of the problems can be solved.
The audit starts at the engineering level
The starting point for the audit is always at the engineering level. You probably already know or suspect this, but in practice, most problems arise due to poor information feedback into design development departments, or lack of vertical integration with other business processes. So whatever the solution, this will need to be addressed at the heart of it.
At this point, the IT guys/gals usually step in. When they are convinced of the potential return-on-investment of changing the way the enterprise operates, they take these financial arguments to senior managers who can authorize and champion the changes. But the battle is not yet won – a negative attitude towards this change at the engineering level can really hamper the process. So it’s important that a positive attitude is created and maintained. You need to win over the hearts and minds of each person, so they appreciate the benefits to the enterprise as a whole – particularly if they personally will be affected by changes in their day-to-day work.
Let’s take Joe Blogs, he is happy doing his day-to-day work and then Mr. Manager steps in and says, ‘sorry pal but we need to change the way you’re doing this because it’s going to save us money.
Maybe in the short term, it is a painful process of learning new methods, taking him out of his comfort zone and causing him stress – naturally he is going to be just a tiny bit resistant (even if he doesn’t admit it to you). Perhaps he has been doing it this way for years and believes that if it’s not broke don’t fix it.
Hey honestly, from his perspective, who can blame him? OK, so take the time out to help him appreciate how much of a positive impact he will be having on the company by doing this.
3) Harmonizing design tools, components, and manufacturing
So the talking, documenting, comparing and general analysis are complete. The next step is harmonizing your design tools, components, and manufacturing. This needs to be company-wide (or else it kind of defeats the point of the change) and a centralized database needs to be created that holds all data, starting with component and library objects.
In parallel, the necessary vertical integration links should be created to other IT systems within the enterprise and an engineering portal should be created to complement existing business portals.
What is the payback?
Of course, no enterprise is going to make such wide-ranging investments and changes to its business processes without the potential for a quantifiable return on investment – I’m talking big bucks.
Over the years my colleagues and I have worked with well over a hundred companies to achieve DAMA capabilities and the initial investment is normally returned within about two years.
Cost savings
But the bottom-line benefits related to cost savings are only part of the story. If you are able to design anywhere and manufacture anywhere you are going to benefit from shorter product development cycles and a reduction of data re-entry and re-creation.
Then think of the physical waste – scrap, rework, and unusable prototypes that will be avoided. If you’re working with expensive materials this is a considerable saving. And then don’t forget the costs that will be reduced relating to…
- components and sub-assemblies
- travel expenses
- shipping and documentation
- manufacturing set-up
- warranty claims
- obsolescence management
I’m sure you can think of lots more cost savings to add to this list…
Be more innovative, achieve better IP re-use creating greater product differentiation
DAMA capability allows you to be more innovative and achieve better IP re-use to create greater product differentiation. Talking marketing and sales now… It means you can be faster to market and gain increased market share. And, with better executive decision making through higher visibility of the organization, communication is improved, wasted time is avoided, employee motivation and retention improves and there is a subsequent reduction in the cost of recruitment and training – that’s as long as you keep them on the side during the change process.
This is one to pass to your CFO and CEO
Perhaps most important of all; the improved flexibility which DAMA provides to an enterprise creates greater customer satisfaction and loyalty and increases both revenues and shareholder value.
Who can argue with that?!
What next
Want to talk more about how this might work for you?
There are lots of options, you can find out more about the technology we have that underpins this – our e-PLM solution DS-2, or maybe you’d like to have a chat?
Then just leave me a message below or talk to your Zuken account manager.
– contact details for your local Zuken office can be found on our website.
You can find links to my other DAMA posts below:
Related Products and Resources
- Products
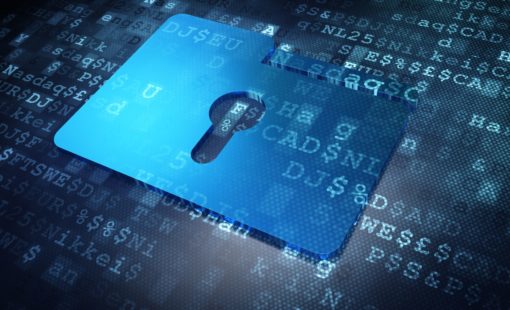
- Products
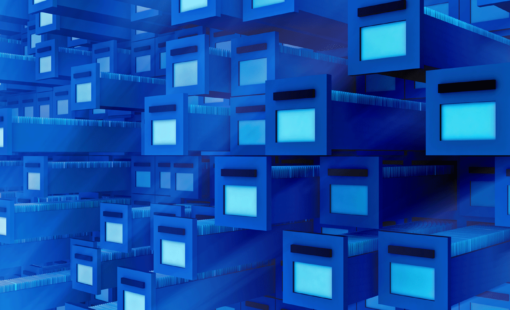
- Products
The traditional practice of mechanical, electrical and electronic engineers working in silos – then consolidating efforts late in the development process – is no longer viable for successful companies. Zuken offers a portfolio of scalable domain data management solutions for PCB and electrical/fluid design plus a range of solutions that integrate design and domain data management into the PLM and ERP world.
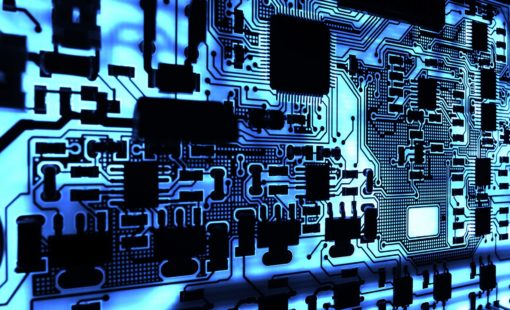
- Products