On September 7, 2022, NASA announced the choice of Axiom Space as the developer and manufacturer of a “moonwalking system” designed for the Artemis 3 mission. A vital part of this assignment includes designing and developing a new generation of spacesuits, possibly similar to those shown in Figure 1, that will support moonwalking for the Artemis 3 mission, which happens to be NASA’s first crewed moon landing in more than 50 years.
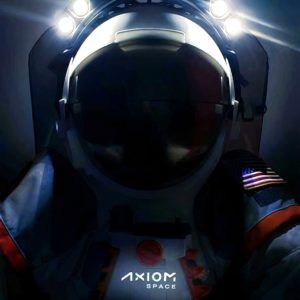
Considering how vastly advanced every other aspect of modern space exploration is, it only makes sense that spacesuits will also undergo an overhaul.
General Spacesuit Requirements
Spacesuits can be explicitly designed for spacewalks or moonwalks, but some designs can serve a dual purpose. Even though spacewalks and moonwalks are significantly different, there are some requirements they have in common, such as being rugged enough to survive factors like extreme temperatures, vacuum pressures, and interactions with sometimes unpredictable environments.
These spacesuits must be highly resistant to damage and provide consistent internal pressurization. There are also factors related to electrical and electronic components. Not only do the parts have to meet stringent requirements to be space-rated, but they also have to be carefully designed and laid out to support extreme reliability and flexibility.
NASA’s Last Moonwalk Suit
As we imagine what the future will look like, it can be illustrative to look back at past designs. As of 2022, the last NASA moonwalk took place in 1972. It was the third moonwalk for the last Apollo mission, and Eugene Andrew Cernan was the “last man on the moon.” The spacesuit, also known as an extravehicular mobility unit, Cernan wore in 1972 was an A7LB model designed and manufactured by the International Latex Corporation.
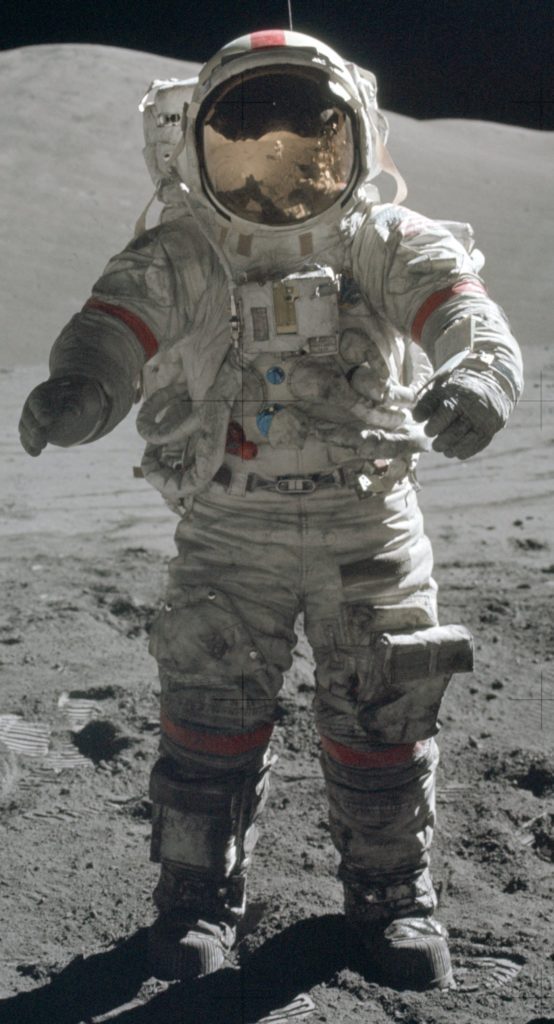
Engineering Next-Generation Spacesuits: A Host of Critical Considerations
According to Michael Suffredini, president and chief executive of Axiom Space, the next-generation suits they will be engineering for NASA will “enable rapid upgrades to implement better, safer technologies over time, ensuring our astronauts are always equipped with high performing, robust equipment.”
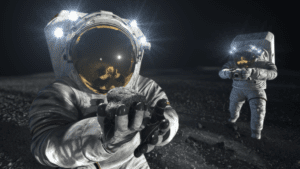
Factors such as SWaP (Space, Weight, and Power) constraints remain vital to the success of space missions and encompass mechanical and electrical designs. And, in common with past designs, there are a host of conditions the new designs must manage and meet. Managing these varying conditions is all but impossible without clear communication between different engineering and manufacturing teams.
Digital design tools and platforms form a crucial part of modern space design. Data and information must be managed and made available among departments for productivity, to meet design milestones on time, to support testing and compliance, and to enable engineers to make the best use of the results of simulations and mock-ups.
In particular, the design of electrical and electronic systems is vital to life support, general safety, performance, and functionality of spacesuits. These systems must meet general design constraints while interacting with mechanical systems, which further reinforces the need for design platforms and tools such as data management, data, and part libraries.
Zuken Space Solutions
Digital design that supports interdisciplinary cooperation and data sharing will be vital for engineering the next generation of spacesuits. Zuken has the products needed to design solutions for space, ranging from satellites to rocket boosters to spacesuits. Our product lines encompass the following:
- Digital engineering
- MBSE (Model-based System Engineering)
- Data and process management
- Electrical design
- Fluid design
- PCB and IC design
PCB Design
For example, Zuken’s CR-8000 3D PCB Design Software fully supports the interdisciplinary design process that combines electronic systems, embedded software development, and mechanical engineering. It spans the PCB engineering lifecycle and is the only product design environment on the market that successfully combines data management capabilities and a comprehensive library along with module, configuration, and release management.
Design Data Management
The Zuken DS-CR PCB Design Data Management tool suite supports organized and accessible workflow information sharing and access to design data specifically for PCB design. This includes design data and configuration management with a multi-site library, all working together to achieve a non-siloed, unified environment for PCB engineering.
The CR-8000 and the DS-CR PCB Design Data Management tools have been used successfully by EREMS, which provides high-tech electronic equipment for space missions, to support the design and lifecycle management of flight electronics for satellites.
Electrical and Wire Harness Design
Zuken’s E3.series electrical design platform supports fluid, power, switchgear, cabling system, wire harness, machinery, and control cabinet designs. This platform has already found success in the space industry: Stone Aerospace used E3.series to save 12 weeks in cabling design, and ATK to boosted their productivity by moving to a digital design process for space shuttle booster cabling, as shown in Figure 4.
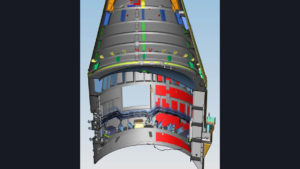
Other solutions include Zuken’s DS-2 Design Data and Workflow Management tool, which makes it possible for companies of any size to achieve multi-disciplinary data sharing from the beginning of the design process rather than consolidating the data towards the end while also supporting PLM (Product Lifecycle Management).
Conclusion
To successfully engineer equipment for use in space, it is critical to manage the product development and production process carefully. It is essential to implement digital design and interdisciplinary data sharing to achieve this. Zuken has the platforms and design tools for the next-generation engineering of spacesuits and more. Contact us today to learn how our knowledge, experience, and products can support your aerospace engineering process.
—
Editorial contributions by EETech
Related Products and Resources
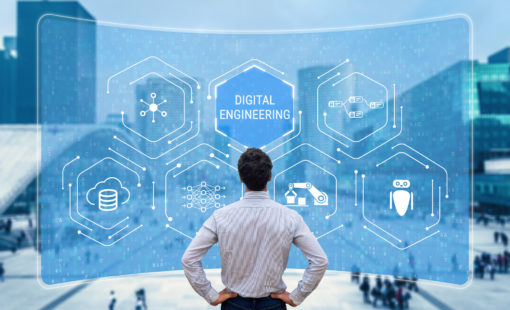
- Solutions
Many companies have recently embarked on the “digital transformation” journey to become more efficient and competitive. A recent IDC study showed that 90% of small and medium-size businesses are budgeting for the digital transformation and 73% have begun the process. According to the survey, the top goal for these companies making the digital transformation journey is to improve product development and design processes.
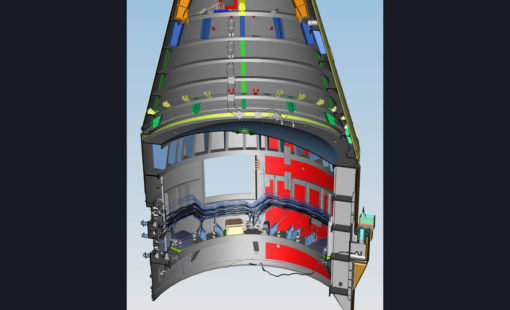
- Success Stories
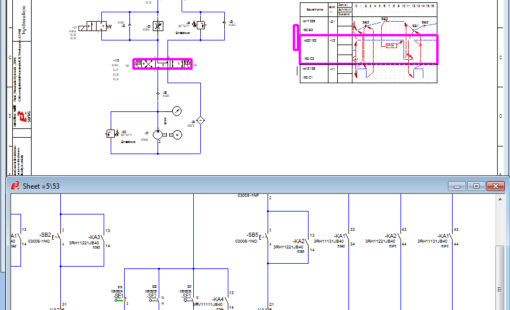
- Products
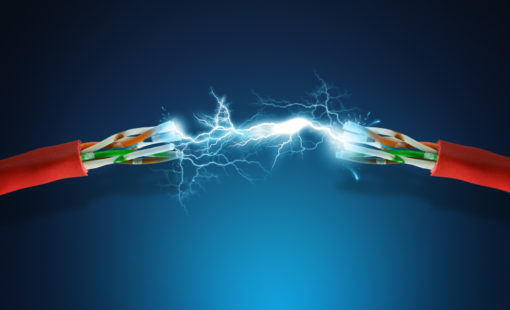
- Products
E3.series is a Windows-based, scalable, easy-to-learn system for the design of wiring and control systems, hydraulics and pneumatics. The out-of-the-box solution includes schematic (for circuit and fluid diagrams), cable (for advanced electrical and fluid design), panel (for cabinet and panel layout), and formboard (for 1:1 wiring harness manufacturing drawings). Integrated with MCAD, E3.series is a complete design engineering solution from concept through physical realization and manufacturing output.