JTAG is an acronym for Joint Test Action Group. It is a powerful and versatile standard that has become integral to electronics testing, debugging, and programming. In this blog post, we’ll explore what JTAG is, its key features, its applications, and how it connects to the broader world of electronic design and testing.
A Brief Overview
JTAG Boundary Scan is a standardized method (IEEE Std 1149.1) for testing the interconnect on printed circuit boards after they have been assembled. Engineers can also use it for In-System-Programming (ISP) of FPGAs and flash memory devices.
JTAG was developed in the 1980s to address the increasing difficulty of testing printed circuit boards. Before JTAG, test fixtures were used to verify interconnects and functionality. However, with surface mount and advanced packaging ( e.g., BGA’s), access to device pins and thru-holes became limited.
Once the BGA is soldered to the board, JTAG utilizes a chain interconnect test to detect manufacturing faults such as shorts or opens. In contrast, a bed-of-nails tester requires physical access to pins via thru-holes, which is unavailable in surface mount technology. Many high-pin count devices today are JTAG-compliant, which enables interconnect testing and improves PCB test coverage. JTAG plays a vital role in today’s electronic manufacturing business.
Key Features and Functions
JTAG operates by using a boundary-scan technique. This method allows for testing the interconnections on printed circuit boards or sub-assemblies without requiring physical access to each component pin. Ball Grid Array (BGA) packages cannot inspect the solder joint visually or physically between the ball and the PCB. An alternative to JTAG for BGA’s is X-raying the PCB, which is costly and time-consuming.
JTAG requires a PCB’s four-pin connector called the Test Access Port (TAP). The TAP contains four signals: TDI (Test Data In), TDO (Test Data Out), TCK (Test Clock), and TMS (Test Mode Select). Utilizing this port, JTAG can perform various functions such as:
- Testing component solder joints for shorts and open circuits.
- In-system programming of FPGAs, CPLDs, and flash devices.
- Debugging embedded systems through access to their memory and processor.
Linking JTAG to Zuken’s Products
Zuken, an electrical and PCB design software leader, integrates JTAG standards into its product offerings. For instance, Zuken’s CR-8000 is a comprehensive PCB design software that supports JTAG-based testing, allowing designers to incorporate testability into their designs from the early stages seamlessly. This integration ensures that products are optimized for performance, manufacturability, and testability, aligning with industry best practices.
Zuken and XJTAG: Revolutionizing PCB Design and Testability
The partnership between Zuken and XJTAG marks a significant milestone in the electronics design and testing landscape. XJTAG has integrated its advanced boundary-scan technology into Zuken’s CR-8000 design suite. This collaboration offers a powerful solution to enhance PCB testability and design efficiency from the earliest stages of development. This strategic alliance streamlines the design-to-production workflow, ensuring higher test coverage. It also reduces the time and cost associated with PCB development.
This integration brings forward the ability to test complex PCB designs more comprehensively, including non-boundary-scan components like SMT connectors, thus ensuring a more thorough verification process. Additionally, it highlights the potential of collaboration in pushing the boundaries of technology, making it a beacon for innovation and efficiency in electronic product design and manufacturing.
Conclusion
JTAG is more than just a testing protocol; it’s a critical tool for designing, manufacturing, and testing modern electronics. Its ability to probe hardware and do in-system programming makes it indispensable in ensuring the quality and reliability of electronic products. As technology continues to evolve, the role of JTAG in facilitating innovation and ensuring product quality is set to grow even further.
Related Products and Resources
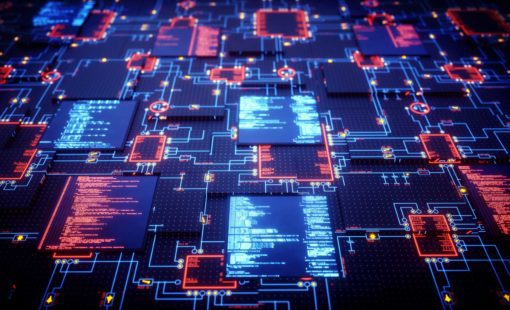
- Blog
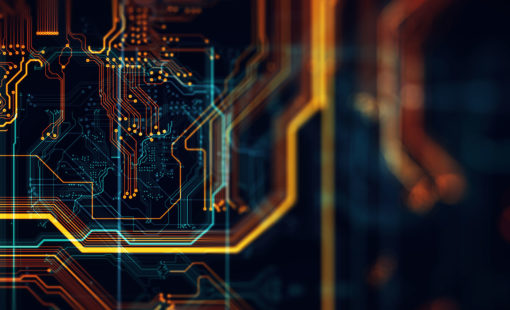
- Products
Building a competitive product today is much more difficult than a few years ago. Existing PCB-centric design processes are limited to a single PCB and do not provide the necessary tools for today’s competitive product development environment. PCB-centric design processes are falling behind.
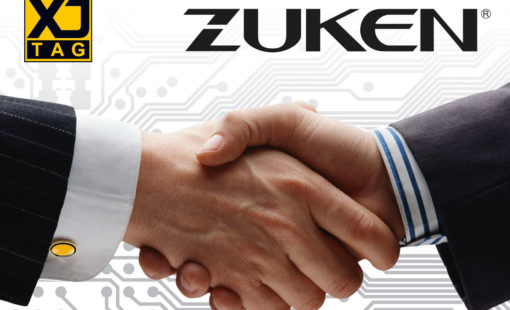
- Press Release