Zuken Reduces Wire Harness Time to Manufacture with Features to Eliminate Manual Errors and Improve Accuracy
Harness Builder 2020 for E3.series is available now
May 13, 2020 – Westford, MA, USA – Harness Builder 2020 for E3.series has been enhanced to provide extended control and processing capabilities for wire harness manufacturers. Harness Builder for E3.series is a packaged solution that allows harness manufacturers to generate accurate customer quotations. From there, the underlying design database can be reused–not reinvented–to create the manufacturable formboard design, saving time, and maintaining the accuracy of the design.
“We’re edging closer to the perfect solution for creating wire harness quotations faster and more accurately while providing the functionality to enter the manufacturing stage much earlier by using the same tool for both jobs”, comments Paul Harvell, Product Director of E3.series.
Auto-placement of device and cable labels
The Auto-placement of device and cable labels, along with heat shrinks, substantially decreases the tedious job of manual measurement and placement on the harness drawing. Labels are dynamically selected based on wire bundle size and auto-placed on connector ends or on the complete harness. The label data becomes part of the system and can be printed locally or sent to industrial label printing machines during the harness assembly process.
User-definable content is extracted directly from the design for printing or exported to vital build documentation eliminating the need to check for compatibility and accuracy of the information against the design.
The new release features auto-placement of tape and/or fixings in predefined positions on nets and set distances from the connector ends. Tape, labels, and heat shrinks are automatically added to the quotation and the bills of materials if required.
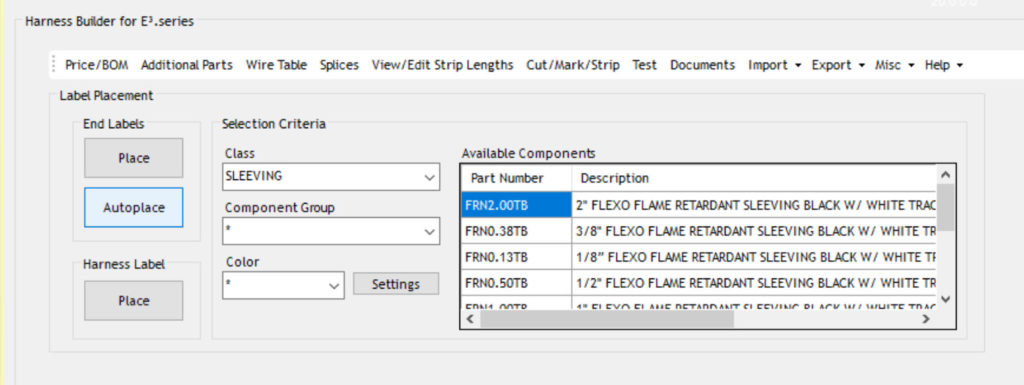
Drafting co-pilot
Harness Builder 2020 for E3.series includes a new drafting co-pilot that allows the user to enter predefined wire or cable lengths. Now a fixed-length cable can be wound around a pin or peg on the formboard, maintaining the predefined length without requiring orthogonal placement. This means a much smaller formboard can be used for building the harness, occupying less space on the manufacturing floor.
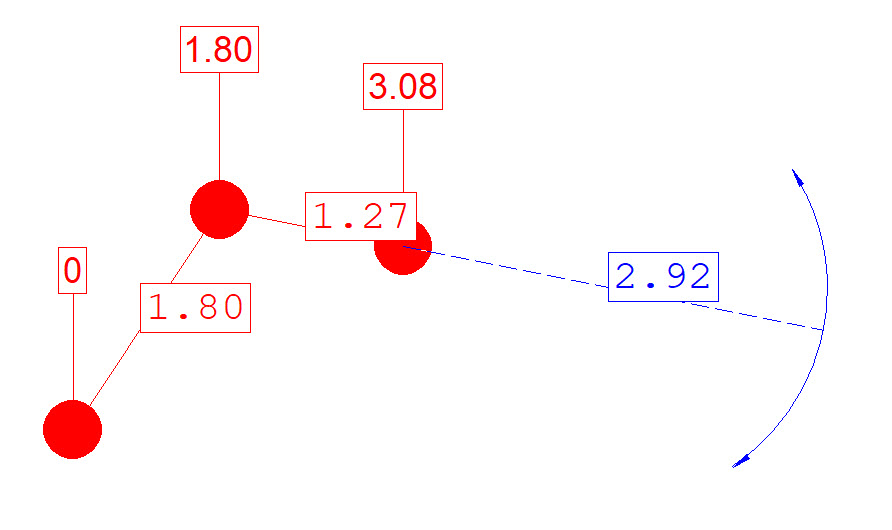
Support for third-party test and manufacturing equipment
Support for third-party test and manufacturing exports has been expanded. Harnesses created with Harness Builder 2020 for E3.series can now be exported directly to CableScan for testing. This integration adds to our growing list of supported vendors that includes Cami Research, Cirris, DIT-MCO, and Dynalab.
Also included in the 2020 release is a new export utility to drive the ProjectionWorks (a division of Delta Sigma) family of manufacturing equipment. Harness placement and wiring information is exported from the Zuken tool and projected directly on the formboard as augmented reality work instructions. This combined solution reduces manual errors and speeds time to manufacture.
Cable tolerancing
Based on feedback from the military sector, Harness Builder 2020 for E3.series now employs a user-driven tolerancing panel, influencing cable lengths. When setting cable tolerancing, this new feature provides the user with a sliding scale of tolerance based on the length and complexity of the cables, improving the overall build accuracy.
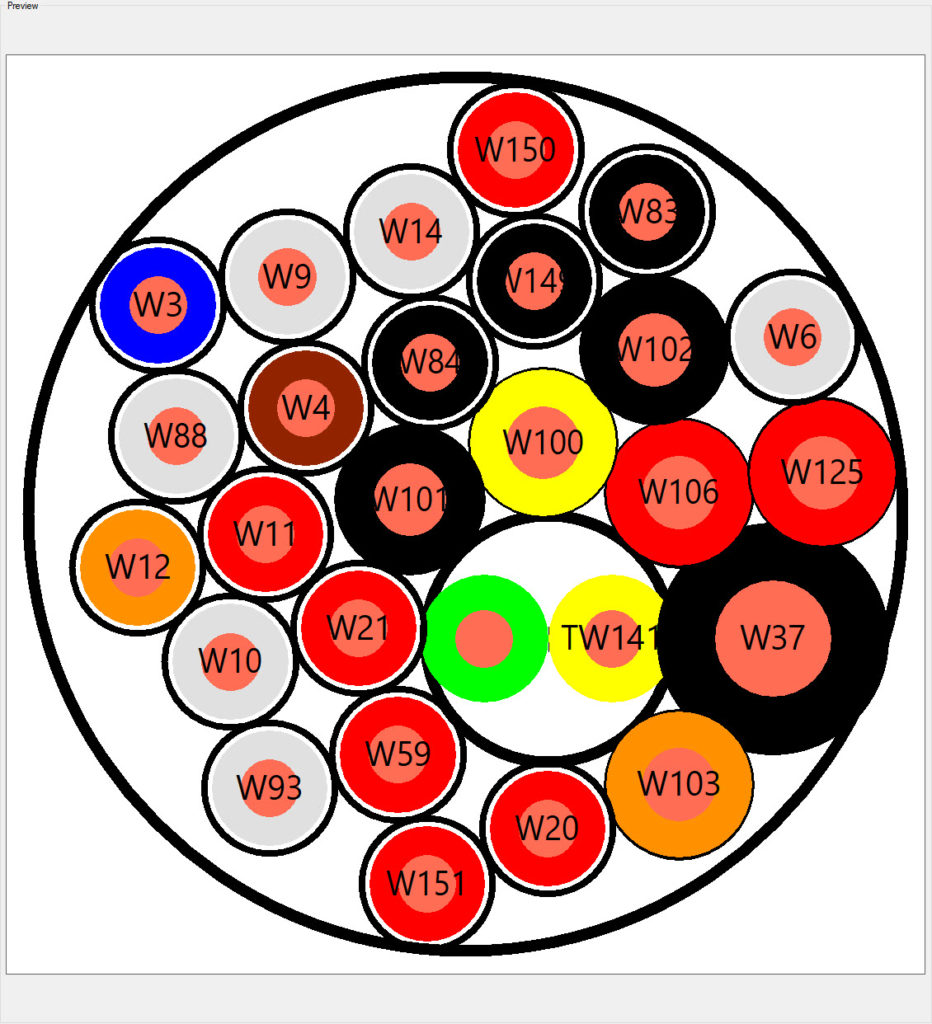
Harness Builder 2020 for E3.series is available now in North America.
For more information, visit https://www.zuken.com/us/resource/e3series-harness-builder-new-release