Abstract
Traditionally, harness and cable engineers combine electrical connectivity and a MCAD 3D model to create documentation for harness manufacturing. Without proper tools, cross-functional collaboration between electrical and mechanical teams can be time-consuming and error-prone.
Additionally, emerging technology in harness manufacturing requires more robust data to drive automation and robotics. An intelligent digital twin is needed to drive modern harness manufacturing solutions, such as machines that cut, mark, and strip wire, harness testing equipment, or even augmented reality assembly systems.
This webinar will discuss the efficiencies of an MCAD 3D flattening flow using E3.3DTransformer. This powerful tool streamlines the integration of electrical connectivity data from Zuken’s E3.series into MCAD tools, facilitating precise physical routing. It also enables the seamless transfer of mechanical data back into E3.series, where harnesses are flattened and formboards are automatically generated for manufacturing documentation. We will highlight the capabilities of E3.formboard and Harness Builder for E3.series, showcasing how E3.series can enhance formboard creation. Utilizing design utilities, report generation, and analysis tools, engineers can significantly reduce errors and streamline the creation of manufacturing documentation. Additionally, by creating the formboard within E3.series, you will develop a robust digital twin. This twin produces automated outputs essential for driving advanced technologies that enhance the efficiency and innovation of wire harness design manufacturing.
What you will learn:
- Transition seamlessly from ECAD to MCAD and back to ECAD.
- Extract harness topological data to E3.series using the E3.3DTransformer.
- Automate features such as flattening and formboard drawing.
- Implement tips and tricks to decrease design time in E3.formboard for harness and cable designs.
- Create BOMs, WRLs, and conduct cost/weight analysis using utilities in Harness Builder for E3.series.
- Generate data inputs for harness manufacturing technologies including wire processing machines, harness testers, and augmented reality assembly systems.
Who should attend:
- Original Equipment Manufacturers
- Harness Manufacturers
- Engineering Directors
Speaker
Geoffrey “Geo” Ng – Applications Engineer, Zuken USA
Geo Ng is an Application Engineer for E3.series, helping implement Zuken solutions that address companies’ electrical design challenges. He focuses on assessing customer needs, educating new users, and improving engineering processes. Geo is a diehard basketball fan and burgeoning board game geek.
Related Products & Resources
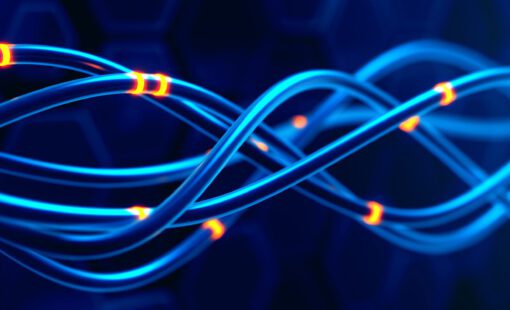
- Products

- Webinar
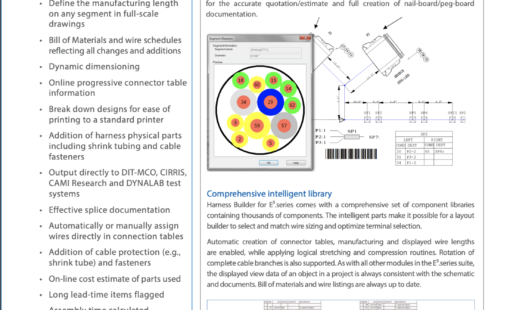
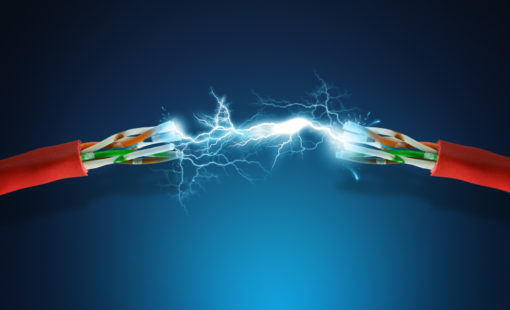
- Products
E3.series is a Windows-based, scalable, easy-to-learn system for the design of wiring and control systems, hydraulics and pneumatics. The out-of-the-box solution includes schematic (for circuit and fluid diagrams), cable (for advanced electrical and fluid design), panel (for cabinet and panel layout), and formboard (for 1:1 wiring harness manufacturing drawings). Integrated with MCAD, E3.series is a complete design engineering solution from concept through physical realization and manufacturing output.