August 5, 11:00 AM CT
Sponsor: Komax Corporation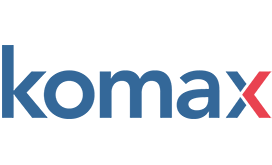
Abstract
The aim of the Smart Cabinet initiative is to find universal solutions for the current and future challenges in control cabinet construction. This involves the interlinking of technology and expertise across all process steps, specifically through the consistent optimization of production processes using all the possibilities offered by digitalization. Only by taking a complete view of the individual aspects of the value creation process can significant efficiency gains be achieved.
“Control cabinet construction, with its still high proportion of manual activities, offers very promising approaches. These range from component selection and the prefabrication of wire harnesses, components, and housings to assisted final assembly and testing prior to commissioning,” explains Matijas Meyer, CEO of the Komax Group.
Author: Tim Crider
Tim Crider is the USA/Canada Sales Director for Komax Corp, responsible for the strategic direction, vision, growth and performance of Sales and Service Teams.
As a seasoned professional with more than 20 years in the industry, Tim is knowing for driving brand growth, maximizing operational excellence, and delivering sales and service performance. Tim brings to his position a well-established background in Sales and Service to ensure growth and complete customer satisfaction.
As Sales Director for Komax Corp, Tim’s goal is to drive portfolio change aligned to meet customer demands. His responsibilities include developing new services offerings and lead with product teams, marketing, sales, and delivery to ensure flawless execution at the region and country levels. Tim holds a degree in BBA from California State University, Fullerton.
Email: Tim.crider@komaxgroup.com
About Komax Corporation:
As the pioneer and market leader for over 40 years, Komax provides its customers with innovative and sustainable solutions for any situation that calls for precision wire processing. Komax manufactures machinery and equipment for various industries, catering to every conceivable degree of automation and customization. Its range of quality tools, test systems, and intelligent networking solutions complete the portfolio and ensure safe and efficient production.
Website