November 19, 2020 – Westford, MA, USA – Zuken Inc., and Electro Magnetic Applications, Inc. (EMA) have entered into a partnership to improve the accuracy of cable harness simulation models for complex electrical subsystems in aircraft and vehicles. The recent collaboration advances Zuken’s digital engineering initiative by enabling design teams to assess, simulate, and validate electrical and electronic designs before they reach manufacturing. This new approach replaces the traditional “design, build, and test” process with a more modern “model, analyze, and build” process resulting in a higher quality product.
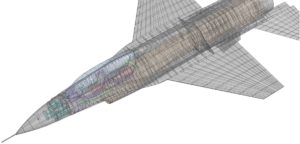
The collaboration between EMA’s EMA3D cable modeling platform and Zuken’s E3.series cable harness design software brings critical detailed design information to the analysis process. Users can now quickly transfer essential design information directly into the EMA3D analysis platform, improving simulation accuracy. Design and safety concerns are more accurately identified and addressed before prototyping, resulting in significant cost and time savings.
Addressing EMC issues at the design stage
Cable harnesses are an integral part of a vehicle or aircraft’s electrical subsystems and are susceptible to external EMI sources such as high intensity radiated fields (HIRF) and lightning strikes. These vehicles or aircraft must undergo extensive electromagnetic compatibility (EMC) certification testing at the physical prototype stage.
EMA3D is a 3D Finite-Difference Time-Domain (FDTD) solver with an integrated multi-conductor transmission line solver. EMA3D is well-suited for simulations that address EMC, HIRF, and lightning strike requirements early in development before physical prototypes are complete.
“EMA3D enables engineers to efficiently analyze complex cable subsystems and evaluate protection schemes for the transportation and aerospace industries,” said Dr. Timothy McDonald, president of EMA. “Collaborating with Zuken to bring the cable harness design details directly into EMA3D will accelerate the time to prototype and improve the level of EMI protection.”
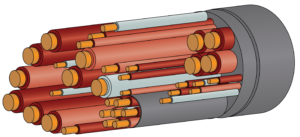
“As products become more and more complex, the ability to access and analyze a design for electrical integrity before manufacturing becomes a basic necessity,” said Kazuhiro Kariya, chief technical officer and managing director of Zuken Inc., Yokohama, Japan. “EMA is the ideal partner to address these challenges with their expertise in the analysis of electromagnetic effects in large systems. Combining Zuken’s E3.series and EMA’s EMA3D platform is an example of digital engineering at its best.”
E3.series is widely used in the manufacturing industry to design large, complex electrical cabling, control cabinet, and wire harness designs for advanced applications in the machinery, power, automotive, transportation, and aerospace and defense industries.
Related Resources
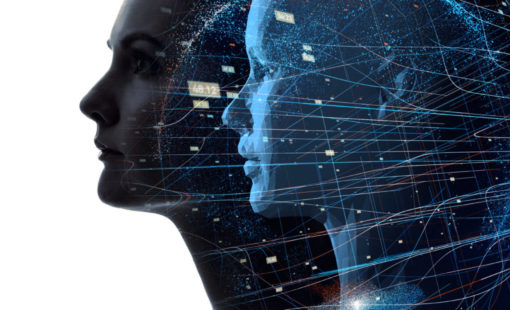
- White Paper
This eBook describes an MBSE based process for Electrical and Electronic design. The eBook begins with model content and structure with the purpose of implementation and the need for a “design envelope”.
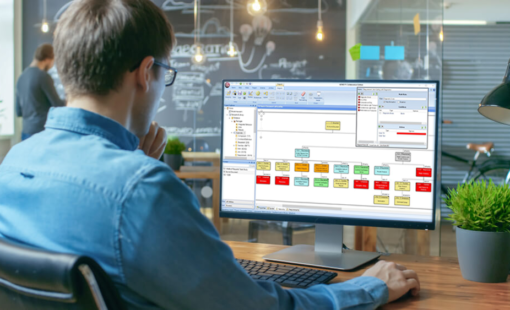
- Products
Digital Engineering requires a model-based design process that begins in Systems Engineering. Zuken acquired Vitech Corporation, a leader in Systems Engineering practices and MBSE solutions, with the intent of implementing an E/E model-based design process.
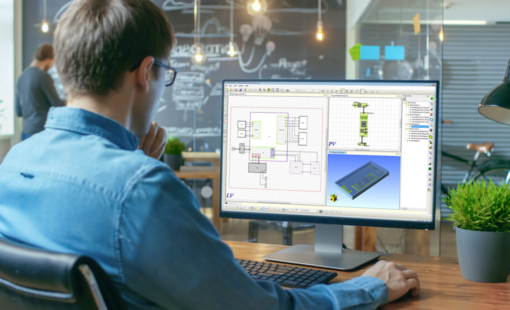
- Products
Digital Engineering requires a model-based design process that begins in Systems Engineering. Zuken acquired Vitech Corporation, a leader in Systems Engineering practices and MBSE solutions, with the intent of implementing an E/E model-based design process.
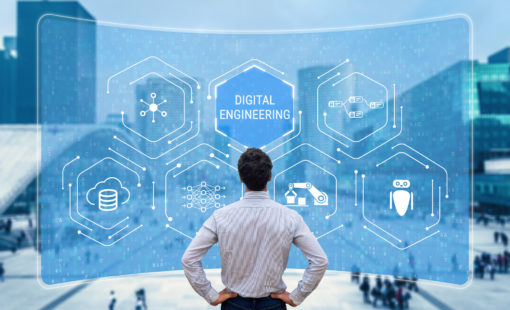
- Solutions
Many companies have recently embarked on the “digital transformation” journey to become more efficient and competitive. A recent IDC study showed that 90% of small and medium-size businesses are budgeting for the digital transformation and 73% have begun the process. According to the survey, the top goal for these companies making the digital transformation journey is to improve product development and design processes.